介紹了兩種典型的噴丸強化方法(氣動式噴丸和離心式噴丸),分別從應用范圍、加工效率、噴射原理、表面完整性等方面對其進行了比較。為揭示噴丸強化機制,概述了噴丸工藝數值模擬與工藝參數優化方法,分析了噴丸對齒根表面完整性影響機制,并闡述了表面完整性參量之間的相互作用關系。同時,闡明了齒輪噴丸后的疲勞斷裂機理,包括裂紋萌生與擴展機制。在此基礎上,重點論述了受噴齒輪彎曲疲勞性能的影響因素,并提出了改善齒輪疲勞強度的措施。此外,簡要探討了齒輪噴丸后,疲勞強度提升幅度問題,并歸納了受噴齒輪彎曲疲勞建模方法。最后,對齒輪齒根噴丸強化工藝進行總結,并對其發展趨勢進行了展望。
齒輪是機械傳動的核心零部件,以汽車齒輪為例,根據功能不同可分為變速箱齒輪、差速器齒輪、車橋齒輪、發動機齒輪等。目前國內常見汽車齒輪鋼有 20CrMnTi、22CrMoH、20CrNiMo、20CrMnMoH 等,而國外常見汽車齒輪鋼主要包括 SAE 4320(美國)、SCr420H(日本)、EN35(英國)、20MnCr5(德國)等。齒輪運行過程中常出現彎曲疲勞與接觸疲勞失效,嚴重影響了齒輪服役壽命。彎曲疲勞失效是交變載荷作用下齒根彎曲應力所致。齒輪在工作時常被視為一支懸臂梁,齒根相當于懸臂梁的支點,齒根圓角處為最大彎曲應力集中區域,疲勞裂紋從此處萌生,若所受載荷較高,且拉應力較大,齒輪會出現早期失效。在齒輪嚙合過程中,受載一側齒根圓角半徑處產生拉應力,而在另一側齒根圓角半徑處受到壓應力。經過多次循環后,在齒根受拉程度最高處,易出現疲勞裂紋,而當齒根承受壓應力時,則不易出現疲勞裂紋。
在交變載荷條件下,齒輪彎曲疲勞失效分為三個階段:第一階段,微裂紋在齒根圓角處萌生;第二階段,裂紋擴展到齒輪內部;第三階段,裂紋迅速延伸擴張,齒輪斷裂,齒根彎曲疲勞失效,如圖 1 所示。接觸疲勞是齒輪接觸區赫茲接觸應力與剪切應力共同作用引起的,其失效形式以點蝕與剝落為主。隨著近幾年汽車行業的高速發展, 輕量化、高承載以及長壽命等高性能齒輪的需求量日益增加,這對齒輪抗疲勞性能提出了更高的要求,因而齒輪表面強化技術顯得尤為重要。
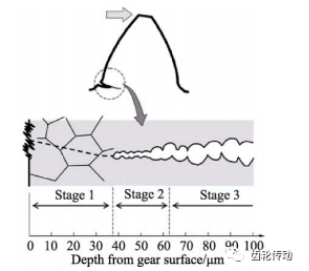
圖 1 齒輪齒根彎曲疲勞失效示意圖
目前大多數汽車齒輪都是采用滲碳、淬火工藝進行表面硬化,可在一定程度上提高齒輪疲勞強度。但齒輪表層殘余壓應力水平較低,疲勞性能提升水平有限,因而只能滿足一般齒輪使用性能要求。噴丸強化技術是一種金屬表面冷加工技術,其工作原理是高硬度、高速運動的彈丸沖擊工件表面,在工件表層引入殘余壓應力。如圖 2 所示,噴丸誘導殘余壓應力抵消了工件外部載荷,從而提高工件抗疲勞性能。噴丸工藝通常與滲碳、淬火等熱處理工藝復合對齒輪進行表面強化,齒輪噴丸后的承載能力可提升 20%~30%。在不需增加齒輪尺寸與重量的情況下,設計人員可通過噴丸提升齒輪承載能力與疲勞強度,并達到節約生產成本的目的。
此外,噴丸的優勢還表現在:1)噴丸誘導殘余壓應力層可防止齒面裂紋與點蝕;2)噴丸引入的彈坑有儲油功能,可提高齒輪潤滑性能,防止齒輪膠合、磨損、剝落發生,以及降低齒輪工作溫度;3)噴丸可消除齒輪機械加工留下的刀痕,減少齒輪表面應力集中;4)噴丸可減少滲碳表層異常組織等。因此,噴丸作為一種提高齒輪疲勞強度、承載能力,并滿足齒輪輕量化設計要求的表面強化工藝,被廣泛應用于齒輪制造領域。
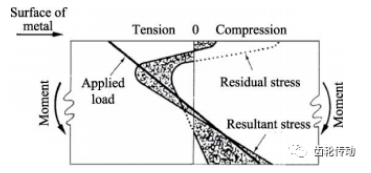
圖 2 外載荷下工件殘余應力
目前,圍繞滲碳齒輪噴丸強化工藝,在工程實踐中,齒根疲勞性能的關注度普遍高于齒面,而且關于齒根噴丸強化的研究報道較多。為促進噴丸強化工藝在滲碳齒輪齒根抗疲勞方面的應用,本文介紹了兩種典型的噴丸強化工藝(氣動式噴丸和離心式噴丸),列舉了其各自特點,并在此基礎上指出了齒輪噴丸工藝選取原則。首先,分析了噴丸工藝數值模擬與工藝參數優化方法,闡述了噴丸對齒根表面完整性(殘余應力、硬度、粗糙度、微觀組織)的作用機制,并探討了表面完整性參量之間的相互作用關系,從而揭示了噴丸強化機理。其次,對噴丸處理齒輪疲勞斷裂機理進行了綜述,重點總結了滲碳齒輪噴丸處理后,影響彎曲疲勞性能的因素,并提出了彎曲疲勞性能改善措施。此外,探討了齒輪噴丸后,彎曲疲勞性能提升幅度問題,并歸納了齒輪噴丸強化后,彎曲疲勞性能建模方法。最后,對齒輪齒根噴丸進行了總結,并對其發展趨勢進行了展望,以期對齒輪噴丸強化工藝的理論研究與實踐應用提供一些參考。在沒有特殊說明的情況下,文中的滲碳代表普通滲碳熱處理。
1 噴丸強化工藝方法
噴丸強化工藝通常包括氣動式噴丸(Air-blast peening)與離心式噴丸(Centrifugal peening),其中離心式噴丸又稱為拋丸。兩者均屬于機械噴丸工藝,最大差異在于噴射動力和方式。氣動式噴丸是利用壓縮空氣驅動丸粒沖擊工件表面;而離心式噴丸工藝是利用葉輪高速旋轉,通過離心力作用將丸粒拋向工件表面。兩者目的均是在工件表面產生殘余壓應力,起到表面強化作用,這與噴砂的用途(工件表面除銹、去除氧化皮)不同。氣動式噴丸與離心式噴丸各有特點,表 1 從噴射方式、丸粒特性、應用范圍、效率等方面,對兩種不同的齒輪噴丸方式進行了對比。由表 1 可見,兩種齒輪噴丸方式并沒有絕對的優劣之分。離心式噴丸方法加工效率高,對大模數齒輪加工優勢突出,但對齒輪外形依賴性大,復雜外形齒輪難以達到均勻覆蓋率;氣動式噴丸可精確控制噴射位置,但加工效率低。因而,選擇噴丸工藝方法時,需根據產能、成本、齒輪外形和尺寸綜合考慮。為集成兩者的優勢,噴-拋丸混合噴丸系統將成為發展趨勢。另外,通過文獻分析可知,相同噴丸工藝參數(彈丸參數、材料參數、設備參數)下,采用上述兩種加工方式所加工齒輪的使用性能之間的對比研究較少。表 1 顯示,相同噴丸工藝參數下,分別采用兩種不同的噴丸工藝所得到的噴丸效果差異明顯。因此,工程實踐中,采用不同噴丸方法欲達到滿意的齒輪噴丸效果,需依據拋噴丸標準,分別設計不同的噴丸工藝參數(例如噴丸強度)。
表 1 噴丸強化方法比較
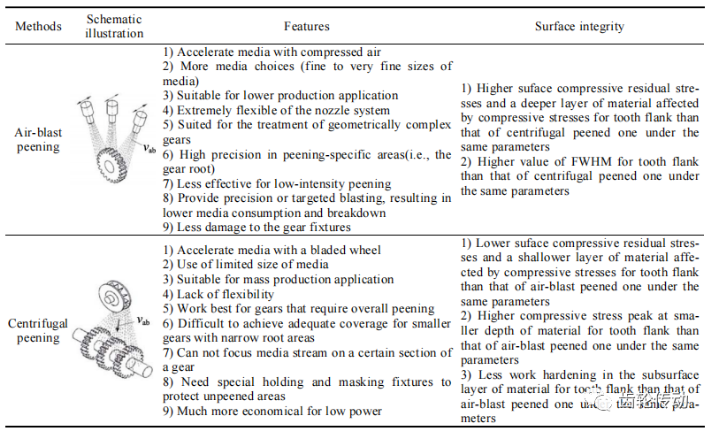
2 噴丸強化數值計算
數值模擬技術為深入揭示噴丸機理提供了強有力支持,可以降低試驗成本,縮短研發周期。噴丸工藝仿真是關于幾何與物理非線性的初值與邊界值求解問題。Comandini 等忽略滲碳引入的殘余壓應力,對 Ni-Cr 滲碳直齒輪噴丸后齒根分別進行了二維與三維殘余應力場數值模擬,仿真模型如圖 3 所示。
結果表明,殘余壓應力峰值仿真結果與試驗結果之間的誤差小于 7%,齒根外表面試驗值大于仿真值。針對齒輪噴丸強化工藝過程中,齒頂邊緣容易出現翻邊,進而影響齒輪嚙合性能,Garijo 等基于 Workbench 有限元分析軟件,提出了一種滲碳直齒圓柱齒輪噴丸后翻邊預測與分析方法,研究表明,噴丸速度、噴嘴相對于齒輪的位置對翻邊的形成影響最大;彈丸流從齒頂向有效齒廓噴射產生的變形量最大,高速彈丸沖擊齒廓邊緣的最大變形量可達 0.024 mm。考慮齒輪滲碳引入的殘余壓應力及噴丸后殘余奧氏體的減少與齒輪表面應變對殘余應力的影響,Inoue 等基于有限元法計算了滲碳直齒輪噴丸后的殘余應力值。Astaraee 等在考慮齒輪復雜幾何特征和梯度材料性能的影響,并忽略噴丸沖擊熱效應的前提下,建立了單丸粒噴丸模型,如圖 4a 所示,采用改變噴丸角度的方法(噴射角變化范圍為 0°~35°),對滲碳直齒輪齒面噴丸后殘余壓應力與粗糙度進行了有限元仿真,得到了 200%覆蓋率下齒面米塞斯應力云圖,如圖 4b 所示。
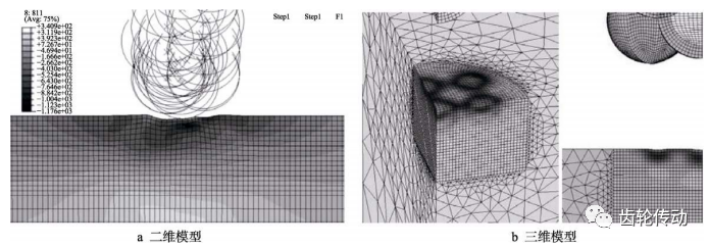
圖3 齒根噴丸仿真
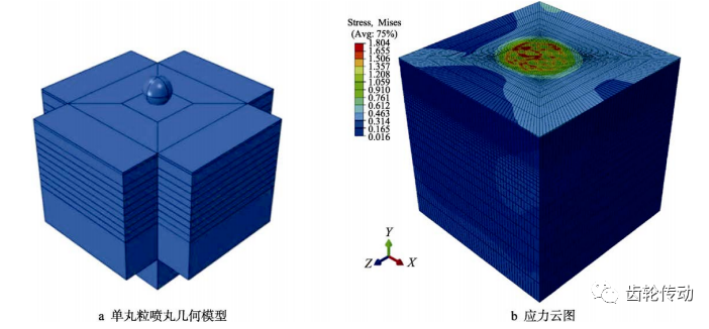
圖 4 齒面噴丸仿真
通過對噴丸強化進行有限元數值模擬,建立噴丸工藝參數與噴丸強化質量表征指標的量化關系,從而實現噴丸強化工藝的優化設計,有助于改善噴丸效果。
但目前噴丸數值計算過程中存在一些不足之處:1)模型過于簡化。齒輪齒根被簡化為平面,而齒根的關鍵區域在齒根圓角處,并非齒底;仿真初始條件忽略滲碳誘導的初始應力場;仿真條件無法包含實際的噴丸工藝參數(噴槍個數、工作臺轉速、噴槍移動速度、彈丸形狀等);噴丸工藝模擬屬于熱力耦合問題,仿真中忽略了熱交換對仿真結果的影響。2)噴丸工藝參數(例如彈丸速度)有時是預設的,因而對噴丸效果只能進行定性分析。3)仿真內容單一。目前研究主要集中于應力場,其他物理場(例如組織場)的仿真研究鮮見報道。4)材料本構模型的精確創建及彈丸速度的確定難度較大。
目前噴丸仿真中比較常用的本構模型包括Chaboche 模型(各向同性,隨動硬化)、Cowper-Symonds 模型(各向同性硬化,考慮應變率效應)、Johnson-Cook 模型(各向同性,考慮應變率效應、加工硬化效應、溫度軟化效應)等。其中,Johnson-Cook 模型形式簡單且參數較少,在齒輪(或齒輪鋼)噴丸工藝仿真中應用最為廣泛。滲碳齒輪鋼本構模型的選擇,不僅要考慮彈丸沖擊過程中材料受到的應變和應變率硬化影響、溫度軟化效應以及材料的循環特性等,還應考慮應變誘導馬氏體相變的影響,因此受噴齒輪材料本構模型有待改進。同時,上述材料本構模型均屬于大應變范圍下的本構模型,對受噴齒輪高周疲勞問題相關研究(例如疲勞壽命估計)并不適用。
目前,彈丸速度確定的方法包括試驗測試法(例如高速相機拍照測量、傳感器測量、光學在線監測系統等)與經驗公式法(例如利用 KIemenz 經驗公式,通過阿爾門強度進行速度建模,通過彈坑尺寸進行速度預測)。其中,經驗公式目前不具備普適性,有些公式只適用于特定噴丸設備、彈丸、阿爾門試片類型等。試驗測量得到的彈丸速度可靠性更高,但無疑會增加測試成本。另外,齒輪具有復雜空間曲面結構,尤其是螺旋錐齒輪齒面法矢、曲率處處變化。噴丸工藝參數相同時,齒輪表面動態沖擊力矢及升熱效應不同,仿真過程中如果要進行簡化處理,勢必會導致誤差的增加。因此,需借助其他軟件(DEFORM、EDEM、YADE、ANSYS 等)進行動力學聯合仿真,完善齒輪噴丸強化工藝數值模擬。
敬請關注下期內容:滲碳齒輪齒根噴丸強化研究現狀與展望(二)