在如今的汽車工業領域內,所使用生產工藝的靈活性已逐漸成為對生產計劃人員的重大挑戰。制造商必須適應不斷變化的零部件范圍。舉例來說,零部件幾何形狀的變化就非常迅速。尤其是在滾齒領域內,這種發展趨勢更是勢頭強勁。以轉向系統部件為例:生產計劃人員需要能對轉向小齒輪、蝸桿和蝸輪進行高效滾齒加工的極其靈活的機床。如何使用一臺機床完成 EPS 轉向系統整個傳動齒輪箱的加工?獨具創新精神的機械制造商能夠完成這項任務。EMAG KOEPFER 最新推出的臥式滾齒機 HLC 150 H 是其中最為優秀的一款機床,是不折不扣的全方位解決方案。這款高效機床可加工的工件范圍極廣:傳動軸、電樞軸、小齒輪以及行星齒輪均可加工,最大長度達500mm。機床具有例如滾齒、刮削滾銑、蝸桿銑削和蝸桿刮削及倒棱等所有相關的滾齒工藝。因此,可以無毛刺加工模數不超過3的各類高品質零部件——滾齒生產靈活性達到了前所未有的高度。
巨大的加工批量、截然不同的工件要求以及從高硬度鋼種類到軟塑料的材料:汽車制造中的齒輪生產是一個非常廣泛并極具挑戰性的領域。有鑒于混合動力驅動系統以及各類輔助系統的廣泛應用,汽車中需要采用滾齒工藝生產的零部件越來越多。因此,最大的問題顯得尤為突出:使用哪種生產解決方案可以高效完整地為盡可能多不同種類的工件進行滾齒加工?
以較低的成本實現全方位的加工
“這正是我們在開始研發機床 HLC 150 H 時的問題”,位于德國菲林根-施文寧根的 EMAG KOEPFER 公司銷售總監Jög Lohmann 解釋說,“針對這一問題,我們研發出了一種采用高性能部件的通用型解決方案。機床上應用了包括倒棱在內的所有相關加工工藝技術,而且機床軸間距達到 130mm,并配備功率高達 28 kW 的刀頭。因此,該機床可以為最大模數 3、齒頂圓直徑最大 150 mm、長度最大 500 mm 的多種工件進行高效滾齒加工。成本的降低和工件質量的提高能為客戶帶來巨大的益處”。“傳動軸”的例子便能清楚說明這一點——HLC 150 H 能夠保證無二次毛刺地完成滾齒加工和倒棱:在第一步對齒輪進行粗加工后,進行擠壓去毛刺加工,并通過第二次滾齒完成最終精加工。最后得到的成果便是無毛刺、已完成倒棱的運行齒輪。同時,使用 HLC 150 H 還能夠降低成本——例如,機床配備的高性能調頻式液壓機組,只有在需要時才會接通介質供應。此外,配備快速夾緊系統的支座以及機床良好的可達性也能保證在最短時間內更換所有刀具。這樣,便能將比如更換批次時的非生產停機時間降至最低。“另外還必須強調其成本優勢,客戶在初期投資時便能從極具吸引力的性價比中獲益”,Lohmann 補充說,“原因在于埃馬克在德國策普斯特和中國金壇均設有高效率的生產基地。具有高效流程的機床的基本結構便分別在這兩個生產基地中誕生”。
確保工件質量
HLC 150 H 的一系列技術細節也讓人印象深刻,正是這些細節保證了工件的高品質和流程的安全性。例如,刀頭采用剛性懸掛方式,并且在銑削加工過程中,只有整個刀頭會移動。兩條軸通過內插方式構成移位軸。由此便可在確保較大銑頭擺動角度的同時,達到較長的竄刀距離。其結果:銑削過程非常平穩和精確。滾齒質量(即使從絕對值測量系統的角度來看)能夠達到最頂級的水平。EMAG KOEPEFR 所采用的切屑處理設計方案也同樣具有重要特性。切屑能自然掉落,不會形成切屑堆積,這個特性能為客戶帶來極大的優勢。因此,機床也非常適合用于干加工。此外,還可以采用例如刮板運輸機或永磁輸送機等多種解決方案送出切屑,也可以選配磁性粗分離輥的深床過濾器,以過濾鐵磁性材料、有色金屬和塑料。“無論采用哪種方式,我們都能確保順利地送出切屑,并保證極高的進程可靠性”,Lohmann 解釋說,“尤其是在高性能大批量生產過程中,這是非常重要的”。
模塊化的工件輸送系統設計方案,范圍廣泛
最后還有很重要的一點,這款機床還可配備一套模塊化的工件輸送系統,能夠確保極短的換裝時間。HLC 150 H 可手動或通過工件輸送系統上料。作為第二種選擇,重量不超過三公斤的輕型工件可使用配備有雙旋轉機械手的內置高速桁架機械手。而對于不超過 10 公斤的重型工件,則可使用 V 型線性機械手。另外,該系統還能夠簡單地整合到埃馬克生產線中。“總而言之,我們可以自豪地說,在靈活加工長度不超過 500 mm 的工件這一領域內,我們的這款機床樹立了一個新的行業標桿。許多轉向系統部件,例如轉向小齒輪、蝸桿和蝸輪以及傳動軸等,都屬于可加工范圍”,Lohmann 總結說,“這款機床集多項優點于一身,例如切削功率高達 28 kW 的刀頭,集成在加工區內、可保證工藝流程的完整性的擠壓去毛刺或倒棱工藝,還有便于整合到生產線中的、極為靈活的工件輸送系統設計方案等。最終的結果便是轉向系統部件或傳動軸的加工成本降低,而質量卻有所上升。我們確信,在汽車制造行業中,HLC 150 H 擁有巨大的市場銷售潛力,必將獲得廣大供應商的青睞!”
圖:HLC150H_1.jpg
EMAG KOEPFER 的 HLC 150 H 可加工長度不超過 500 mm、模數不超過 3 的多種工件。
圖:HLC150H_2
工件輸送系統可選配雙旋轉機械手的高速桁架機械手,或者采用 V 型線性機械手。
Bild:HLC150H_3 & HLC150H_4
加工區概覽:達到 130 mm 的機床軸間距以及功率高達 28 kW 的刀頭,確保靈活性和高效性。
巨大的加工批量、截然不同的工件要求以及從高硬度鋼種類到軟塑料的材料:汽車制造中的齒輪生產是一個非常廣泛并極具挑戰性的領域。有鑒于混合動力驅動系統以及各類輔助系統的廣泛應用,汽車中需要采用滾齒工藝生產的零部件越來越多。因此,最大的問題顯得尤為突出:使用哪種生產解決方案可以高效完整地為盡可能多不同種類的工件進行滾齒加工?
以較低的成本實現全方位的加工
“這正是我們在開始研發機床 HLC 150 H 時的問題”,位于德國菲林根-施文寧根的 EMAG KOEPFER 公司銷售總監Jög Lohmann 解釋說,“針對這一問題,我們研發出了一種采用高性能部件的通用型解決方案。機床上應用了包括倒棱在內的所有相關加工工藝技術,而且機床軸間距達到 130mm,并配備功率高達 28 kW 的刀頭。因此,該機床可以為最大模數 3、齒頂圓直徑最大 150 mm、長度最大 500 mm 的多種工件進行高效滾齒加工。成本的降低和工件質量的提高能為客戶帶來巨大的益處”。“傳動軸”的例子便能清楚說明這一點——HLC 150 H 能夠保證無二次毛刺地完成滾齒加工和倒棱:在第一步對齒輪進行粗加工后,進行擠壓去毛刺加工,并通過第二次滾齒完成最終精加工。最后得到的成果便是無毛刺、已完成倒棱的運行齒輪。同時,使用 HLC 150 H 還能夠降低成本——例如,機床配備的高性能調頻式液壓機組,只有在需要時才會接通介質供應。此外,配備快速夾緊系統的支座以及機床良好的可達性也能保證在最短時間內更換所有刀具。這樣,便能將比如更換批次時的非生產停機時間降至最低。“另外還必須強調其成本優勢,客戶在初期投資時便能從極具吸引力的性價比中獲益”,Lohmann 補充說,“原因在于埃馬克在德國策普斯特和中國金壇均設有高效率的生產基地。具有高效流程的機床的基本結構便分別在這兩個生產基地中誕生”。
確保工件質量
HLC 150 H 的一系列技術細節也讓人印象深刻,正是這些細節保證了工件的高品質和流程的安全性。例如,刀頭采用剛性懸掛方式,并且在銑削加工過程中,只有整個刀頭會移動。兩條軸通過內插方式構成移位軸。由此便可在確保較大銑頭擺動角度的同時,達到較長的竄刀距離。其結果:銑削過程非常平穩和精確。滾齒質量(即使從絕對值測量系統的角度來看)能夠達到最頂級的水平。EMAG KOEPEFR 所采用的切屑處理設計方案也同樣具有重要特性。切屑能自然掉落,不會形成切屑堆積,這個特性能為客戶帶來極大的優勢。因此,機床也非常適合用于干加工。此外,還可以采用例如刮板運輸機或永磁輸送機等多種解決方案送出切屑,也可以選配磁性粗分離輥的深床過濾器,以過濾鐵磁性材料、有色金屬和塑料。“無論采用哪種方式,我們都能確保順利地送出切屑,并保證極高的進程可靠性”,Lohmann 解釋說,“尤其是在高性能大批量生產過程中,這是非常重要的”。
模塊化的工件輸送系統設計方案,范圍廣泛
最后還有很重要的一點,這款機床還可配備一套模塊化的工件輸送系統,能夠確保極短的換裝時間。HLC 150 H 可手動或通過工件輸送系統上料。作為第二種選擇,重量不超過三公斤的輕型工件可使用配備有雙旋轉機械手的內置高速桁架機械手。而對于不超過 10 公斤的重型工件,則可使用 V 型線性機械手。另外,該系統還能夠簡單地整合到埃馬克生產線中。“總而言之,我們可以自豪地說,在靈活加工長度不超過 500 mm 的工件這一領域內,我們的這款機床樹立了一個新的行業標桿。許多轉向系統部件,例如轉向小齒輪、蝸桿和蝸輪以及傳動軸等,都屬于可加工范圍”,Lohmann 總結說,“這款機床集多項優點于一身,例如切削功率高達 28 kW 的刀頭,集成在加工區內、可保證工藝流程的完整性的擠壓去毛刺或倒棱工藝,還有便于整合到生產線中的、極為靈活的工件輸送系統設計方案等。最終的結果便是轉向系統部件或傳動軸的加工成本降低,而質量卻有所上升。我們確信,在汽車制造行業中,HLC 150 H 擁有巨大的市場銷售潛力,必將獲得廣大供應商的青睞!”
圖:HLC150H_1.jpg
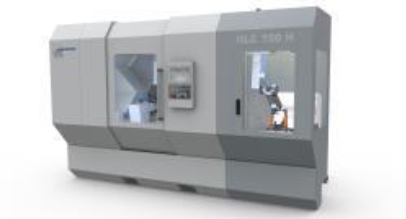
EMAG KOEPFER 的 HLC 150 H 可加工長度不超過 500 mm、模數不超過 3 的多種工件。
圖:HLC150H_2
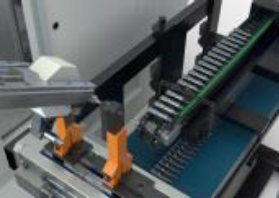
工件輸送系統可選配雙旋轉機械手的高速桁架機械手,或者采用 V 型線性機械手。
Bild:HLC150H_3 & HLC150H_4
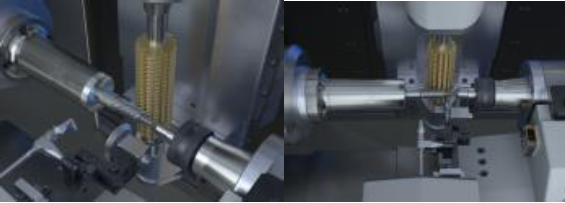
加工區概覽:達到 130 mm 的機床軸間距以及功率高達 28 kW 的刀頭,確保靈活性和高效性。