航空殼體類零件主要應用于航空產品的液壓傳動及機械傳動裝置,是產品的核心零部件。其不僅是產品裝配 母 體,更是產品功能實現的樞紐部位。該零件的復 合 程 度 高,殼體材料多以鋁合金為主。其按結構特點可劃分為作動類殼體、薄壁類殼體、液壓類殼體及其他類殼體。由于大多數航空殼體具有料去除率高、單道工序加工時間長和所采用的刀具種類多等特點,因而殼體類零件適合采用高速切削,以提高加工效率。
刀具以及相關系統對于高速切削有著重要的影響。本文對刀具幾何參數、刀具夾持系統以及加工工藝等影響因素進行研究分析。
1、 高速切削
高速切削(HSM 或 HSC)是20世紀90年代迅速走向實際應用的先進加工技術,通常指在高主軸轉速和高進給情況下進行切削。國際生產工程學會提出,高 速 切 削 的 切 削 線 速 度 為 500——7000 m/min[1]。在模具 加 工 中,高 速 切 削 可 加 工 淬 火 硬 度>50HRC的鋼件。高速切削是一項系統技術,從刀具材 料、刀
2 、刀具對高速切削的影響分析
2.1 刀具幾何參數
目前,高速切削鋁合金刀具多采用硬質合金刀具,粗加工刀具具有良好的強度及排屑性能,適用于大余量去除材料;精加工刀具具有良好的刃口鋒利性和較小的徑向力,適用于減少加工變形,降低表面粗糙度。刀具主要參數為前、后角和螺旋角,高速切削刀具與普通刀具幾何參數的區別主要為柄部公差、螺旋角和刀具跳動(見表1)。
2.2 刀具材料
按照刀具材料硬度大小排列如下:金剛石 PCD>立方氮 化 硼 PCBN> 陶瓷 > 硬 質 合 金 > 高 速 鋼HSS;按照抗彎強度大小排列如下:高速鋼 HSS>硬質合金>陶瓷>金剛石PCD>立方氮化硼 PCBN;按照斷裂韌性大小排列如下:高速鋼 HSS>硬質合金>立方氮化硼 PCBN>金剛石 PCD>陶瓷。根據切削
材料以及刀具成本等方面綜合考慮,現階段航空企業高速切削鋁合金多以硬質合金材料為主。
硬質合金刀具種類按照化學成分不同,可分為碳化鎢基硬質合金和碳化鈦基硬質合金;按照晶粒大小區分,可分為普通硬質合金、細晶粒硬質合金和超細晶粒硬質合金。硬質合金顆粒的大小影響到合金材料的強度,普通硬質合金晶粒度為3——5μm;一般細晶粒硬質合金的晶粒度約為1.5μm;亞微細晶粒硬質合金的晶粒度為0.5——1μm;超細晶粒硬質合金 WC 的晶粒度<0.5μm。晶粒細化后 可 以 提高合金的硬度、耐磨性、抗彎強度和抗崩刃性。K 類和 M 類硬質合金具有較高的硬度、耐 用 度、抗 彎 強度和韌度,細晶粒和超細晶粒硬質合金中由于硬質相和粘結相高度分散,可減少切削時產生的崩刃情況,適合于高速切削鋁合金[7]。適合高速切 削 的 硬質合金材料見表2。
2.3 刀柄結構
刀具的夾持系統為刀柄,按照與機床連接方式,刀柄分為7∶24和1∶10等2種。在傳 統 的 加 工中,通常使用的是7∶24的刀柄。這種刀柄端面與主軸端面之間存在間隙,在主軸高速旋轉和切削力的作用下,主軸的大端孔徑膨脹,造成刀具軸向和徑向定位精 度 下 降。高速切削通常推薦 HSK 刀柄。HSK 是一種小錐度(1∶10)的空心短錐柄,使用時端面和錐面同時接觸,從而形成高的接觸剛度,高轉速對接口的連接剛度影響不大。在高速切削中,刀柄對刀具的夾持力的大小和夾持精度的高低具有十分重要的作用。當機床轉速達到10000r/min時,應采用夾持可靠的刀柄。目前,加工中常用的刀柄為側固刀柄、卡簧刀柄、液壓刀柄和熱脹刀柄等,側固式刀柄難以保證刀具的動平衡,不適用于高速切削;卡簧刀柄采用彈性夾緊方式,刀柄與刀具中間存在彈性夾頭的過渡,會影響刀具的跳動和動平衡,不適用于高速切削;液壓刀柄采用兩點夾持的一體型構造,具有很高的夾持力和夾持精度,且減小了夾頭質量;熱脹刀柄利用刀柄裝刀孔熱脹冷縮使刀具夾緊可靠,其結構簡單對稱、夾緊力大。可見,液壓刀柄和熱脹刀柄適用于高速切削。
2.4 刀具的動平衡及安全性
高速切削設備的主軸轉速一般可達到15000——24000r/min。刀具在高速旋轉時存在的殘余不平衡量會產生與轉速成平方關系的離心力,這種動態負載會激起刀具和機床的振動,從而導致加工表面質量、刀具壽命和主軸軸承壽命下降。刀具系統不平衡的主要因素如下:1)刀具制造尺寸精度偏差導致不平衡;2)非對稱式刀具、刀柄以及連接件導致不平衡;3)刀具使用時產生偏移導致不平衡;4)非整體式刀具系統裝配時的累積誤差導致不平衡;5)刀具裝夾誤差導致不平衡。
為減小或限制這種由殘余不平衡量產生的動態負載的影響,應對主軸及刀具系統進行必要的動平衡調整。刀具動平衡分為機外平衡和機上平衡,機上動平衡利用機床主軸提供旋轉運動,其余與機外動平衡機相同。現階段動平衡檢查主要以機外平衡為主。機外動平衡需通過專用機外動平衡機測量出不平衡的質量和相位,再通過技術手段進行調整,使刀具系統達到平衡標準要求。動平衡調整過程通常須經過多次反復,調整到最佳平衡量,以減小振動負載,并盡可能將較高的精度傳遞到刀具的切削刃。
2.5 切削路徑
采取不同的切削路徑能得到不同的切削效果。優化切削路徑可提高刀具耐用度和切削效率,獲得最小的加工變形,充分發揮高速切削的優勢。本文從進、退刀加工和刀具軌跡2個方面進行分析。
1)進、退刀加工。在加工進刀時,應避免刀具垂直插入工件,采用傾斜下刀方式或者螺旋式下刀,以降低刀具載荷。在加工平面或輪廓時,應盡量從工件外部下刀,然后水平切入工件。在水平退刀時,應盡量保持加工進給速度,當刀具垂直退出時可采用最大位移速度。
2)刀具軌跡。在高速切削時應保證刀具軌跡盡可能簡化,減少轉折點和急速轉向,保證刀具軌跡的平滑過渡。螺旋曲線走刀是高速切削加工中一種較為有效的走刀方式。另外,應通過不中斷切削過程和刀具路徑,減少刀具的切入和切出次數,以獲得穩定、高效和高精度的切削過程[8]。
2.6 切削參數
切削參數是高速切削中重要的指標之一,切削參數選擇是否合理將直接影響最終的加工效率、加工表面質量以及加工成本。
切削速度取決于機床的性能,采用較高的切削速度可以減少加工過程中的積屑瘤,提高表面加工質量;但是過高的切削速度會加劇刀具磨損,降低刀具壽命。所以在零件切削過程中需要根據現場的加工環境選擇合適的切削速度。
進給量是影響加工效率的主要因素,在粗加工過程中,選用較高的進給量能夠獲得較大的材料去除率。進給量與刀具的直徑相關,每齒進給量隨直徑增 大 而 增 加。粗加工時每齒進給量推薦 0.1——0.3mm;精加工時每齒進給量推薦0.04——0.1mm。軸向切深和徑向切寬在粗加工時根據刀具直徑和機床的剛度所決定。一般在選用刀尖圓弧半徑較大的刀具時,軸向切深不宜大于刀具半徑;徑向切深與被加工材料相關,對于鋁合金等輕合金材料可以選擇較大的徑向切深,甚至滿刀切削。
3 、某葉輪加工應用實例
3.1 葉輪結構
葉輪類零件屬于薄壁、易變形類零件,一般壁≤4mm。本次試加工葉輪為離心壓縮機中應用的非直紋面葉輪(見圖2),其共有14片葉片,直徑 為60mm,高度為18mm。葉片厚度為1mm,葉片間距最小為1mm。葉輪材料為7A04。
由于受體積限制,葉輪采用小直徑、大扭角的結構,這給葉片的加工帶來了更高的難度:整體葉輪加工流道窄,葉片相對長,葉片間距最小處≤1.5mm,一般需要采用小刀具直徑加工,加工過程中易造成刀具斷裂。
3.2 刀具切削參數的選用
選用SECO 的極 小 徑 系 列 刀 具,選 用4和2mm 刀具進行粗加工;1.2mm 刀具進行半精加工留余量0.1mm;1mm 刀具 進 行 精 加 工。精 加 工刀具為錐桿結構,切削刃末端為縮頸,該結構在讓開干涉的同時最大限度地提高了刀具強度,保證了加工穩 定 性。刀 柄 采 用 HSK——A63 熱脹 刀 柄 夾 持。切削參數見表3。
3.3 走刀過程
本次加工使用 CATIA 軟件編制加工程序。粗加工采用插銑加工方法,刀具沿葉片各角度的切線方向對葉輪進行插銑加工。插銑粗加工的優點如下:1)由于切削力為軸向力,可采用大懸伸避免干涉;2)可減小工件變形;3)提高加工效率。粗加工插銑采用 定 軸3+2方式 進 行 分 層 加 工(見 圖 3)。在 CATIA 軟件中 選 擇 等 高 降 層 粗 銑 策 略,以 流 道輪廓為限制線,兩側葉頂為干涉面,刀軸方向以一次策略為單位多次旋轉,以達到讓開干涉,去除大余量的目的。
精加工中,流道底部按照3個區域分別拾取加工面,使用曲面等參數線加工策略,選擇插補軸的多軸方式,以區域邊界多個驅動軸為刀軸方向,通過手動設置適應 曲 率 變 化,形 成 整 齊、穩定和高效的刀路。主葉片吸力面、主葉片壓力面、分流葉片吸力面和分流葉片壓力面分別采用同樣的策略,以無干涉、無跳刀和加工完整為目的,以區域邊界的25個驅動軸為刀軸方向,通過手動設置來適應劇烈的曲率變化,生成整齊可靠的刀路(見圖4)。
4、 結語
高速切削已經在航空領域得到廣泛應用,本文從刀具結構、刀具幾何參數、刀具夾持系統以及加工工藝等影響因素進行分析,并結合航空殼體零件在實際加工中的應用實例,進一步掌握刀具在高速切削中的影響,從而提升高速切削的應用效果,降低加工成本。
柄、機床、控制系統和加工工藝等方面均與常規加工有很大區別。由于不同的加工方式、不同的工件材料有不同的高速切削范圍,因而應根據不同的加工材料,結 合 實 際 生 產 情 況,確 定 合 理 的 高 速 切 削 范圍[2——6]。高速切削的速度范圍與被加工材料的關系如圖1所示。
刀具以及相關系統對于高速切削有著重要的影響。本文對刀具幾何參數、刀具夾持系統以及加工工藝等影響因素進行研究分析。
1、 高速切削
高速切削(HSM 或 HSC)是20世紀90年代迅速走向實際應用的先進加工技術,通常指在高主軸轉速和高進給情況下進行切削。國際生產工程學會提出,高 速 切 削 的 切 削 線 速 度 為 500——7000 m/min[1]。在模具 加 工 中,高 速 切 削 可 加 工 淬 火 硬 度>50HRC的鋼件。高速切削是一項系統技術,從刀具材 料、刀
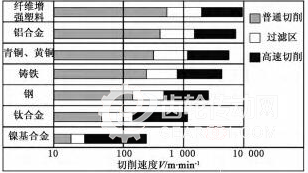
圖1 不同加工材料大致的切削速度范圍
2 、刀具對高速切削的影響分析
2.1 刀具幾何參數
目前,高速切削鋁合金刀具多采用硬質合金刀具,粗加工刀具具有良好的強度及排屑性能,適用于大余量去除材料;精加工刀具具有良好的刃口鋒利性和較小的徑向力,適用于減少加工變形,降低表面粗糙度。刀具主要參數為前、后角和螺旋角,高速切削刀具與普通刀具幾何參數的區別主要為柄部公差、螺旋角和刀具跳動(見表1)。
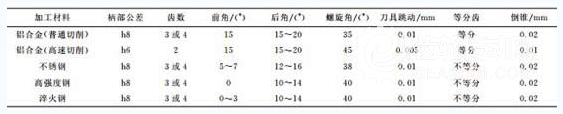
表1 不同加工材料的刀具幾何參數
2.2 刀具材料
按照刀具材料硬度大小排列如下:金剛石 PCD>立方氮 化 硼 PCBN> 陶瓷 > 硬 質 合 金 > 高 速 鋼HSS;按照抗彎強度大小排列如下:高速鋼 HSS>硬質合金>陶瓷>金剛石PCD>立方氮化硼 PCBN;按照斷裂韌性大小排列如下:高速鋼 HSS>硬質合金>立方氮化硼 PCBN>金剛石 PCD>陶瓷。根據切削
材料以及刀具成本等方面綜合考慮,現階段航空企業高速切削鋁合金多以硬質合金材料為主。
硬質合金刀具種類按照化學成分不同,可分為碳化鎢基硬質合金和碳化鈦基硬質合金;按照晶粒大小區分,可分為普通硬質合金、細晶粒硬質合金和超細晶粒硬質合金。硬質合金顆粒的大小影響到合金材料的強度,普通硬質合金晶粒度為3——5μm;一般細晶粒硬質合金的晶粒度約為1.5μm;亞微細晶粒硬質合金的晶粒度為0.5——1μm;超細晶粒硬質合金 WC 的晶粒度<0.5μm。晶粒細化后 可 以 提高合金的硬度、耐磨性、抗彎強度和抗崩刃性。K 類和 M 類硬質合金具有較高的硬度、耐 用 度、抗 彎 強度和韌度,細晶粒和超細晶粒硬質合金中由于硬質相和粘結相高度分散,可減少切削時產生的崩刃情況,適合于高速切削鋁合金[7]。適合高速切 削 的 硬質合金材料見表2。
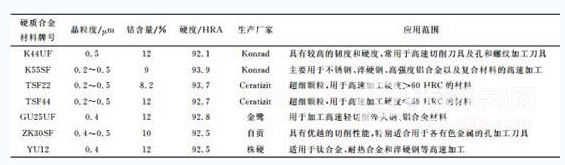
表2 適合高速切削的硬質合金材料
2.3 刀柄結構
刀具的夾持系統為刀柄,按照與機床連接方式,刀柄分為7∶24和1∶10等2種。在傳 統 的 加 工中,通常使用的是7∶24的刀柄。這種刀柄端面與主軸端面之間存在間隙,在主軸高速旋轉和切削力的作用下,主軸的大端孔徑膨脹,造成刀具軸向和徑向定位精 度 下 降。高速切削通常推薦 HSK 刀柄。HSK 是一種小錐度(1∶10)的空心短錐柄,使用時端面和錐面同時接觸,從而形成高的接觸剛度,高轉速對接口的連接剛度影響不大。在高速切削中,刀柄對刀具的夾持力的大小和夾持精度的高低具有十分重要的作用。當機床轉速達到10000r/min時,應采用夾持可靠的刀柄。目前,加工中常用的刀柄為側固刀柄、卡簧刀柄、液壓刀柄和熱脹刀柄等,側固式刀柄難以保證刀具的動平衡,不適用于高速切削;卡簧刀柄采用彈性夾緊方式,刀柄與刀具中間存在彈性夾頭的過渡,會影響刀具的跳動和動平衡,不適用于高速切削;液壓刀柄采用兩點夾持的一體型構造,具有很高的夾持力和夾持精度,且減小了夾頭質量;熱脹刀柄利用刀柄裝刀孔熱脹冷縮使刀具夾緊可靠,其結構簡單對稱、夾緊力大。可見,液壓刀柄和熱脹刀柄適用于高速切削。
2.4 刀具的動平衡及安全性
高速切削設備的主軸轉速一般可達到15000——24000r/min。刀具在高速旋轉時存在的殘余不平衡量會產生與轉速成平方關系的離心力,這種動態負載會激起刀具和機床的振動,從而導致加工表面質量、刀具壽命和主軸軸承壽命下降。刀具系統不平衡的主要因素如下:1)刀具制造尺寸精度偏差導致不平衡;2)非對稱式刀具、刀柄以及連接件導致不平衡;3)刀具使用時產生偏移導致不平衡;4)非整體式刀具系統裝配時的累積誤差導致不平衡;5)刀具裝夾誤差導致不平衡。
為減小或限制這種由殘余不平衡量產生的動態負載的影響,應對主軸及刀具系統進行必要的動平衡調整。刀具動平衡分為機外平衡和機上平衡,機上動平衡利用機床主軸提供旋轉運動,其余與機外動平衡機相同。現階段動平衡檢查主要以機外平衡為主。機外動平衡需通過專用機外動平衡機測量出不平衡的質量和相位,再通過技術手段進行調整,使刀具系統達到平衡標準要求。動平衡調整過程通常須經過多次反復,調整到最佳平衡量,以減小振動負載,并盡可能將較高的精度傳遞到刀具的切削刃。
2.5 切削路徑
采取不同的切削路徑能得到不同的切削效果。優化切削路徑可提高刀具耐用度和切削效率,獲得最小的加工變形,充分發揮高速切削的優勢。本文從進、退刀加工和刀具軌跡2個方面進行分析。
1)進、退刀加工。在加工進刀時,應避免刀具垂直插入工件,采用傾斜下刀方式或者螺旋式下刀,以降低刀具載荷。在加工平面或輪廓時,應盡量從工件外部下刀,然后水平切入工件。在水平退刀時,應盡量保持加工進給速度,當刀具垂直退出時可采用最大位移速度。
2)刀具軌跡。在高速切削時應保證刀具軌跡盡可能簡化,減少轉折點和急速轉向,保證刀具軌跡的平滑過渡。螺旋曲線走刀是高速切削加工中一種較為有效的走刀方式。另外,應通過不中斷切削過程和刀具路徑,減少刀具的切入和切出次數,以獲得穩定、高效和高精度的切削過程[8]。
2.6 切削參數
切削參數是高速切削中重要的指標之一,切削參數選擇是否合理將直接影響最終的加工效率、加工表面質量以及加工成本。
切削速度取決于機床的性能,采用較高的切削速度可以減少加工過程中的積屑瘤,提高表面加工質量;但是過高的切削速度會加劇刀具磨損,降低刀具壽命。所以在零件切削過程中需要根據現場的加工環境選擇合適的切削速度。
進給量是影響加工效率的主要因素,在粗加工過程中,選用較高的進給量能夠獲得較大的材料去除率。進給量與刀具的直徑相關,每齒進給量隨直徑增 大 而 增 加。粗加工時每齒進給量推薦 0.1——0.3mm;精加工時每齒進給量推薦0.04——0.1mm。軸向切深和徑向切寬在粗加工時根據刀具直徑和機床的剛度所決定。一般在選用刀尖圓弧半徑較大的刀具時,軸向切深不宜大于刀具半徑;徑向切深與被加工材料相關,對于鋁合金等輕合金材料可以選擇較大的徑向切深,甚至滿刀切削。
3 、某葉輪加工應用實例
3.1 葉輪結構
葉輪類零件屬于薄壁、易變形類零件,一般壁≤4mm。本次試加工葉輪為離心壓縮機中應用的非直紋面葉輪(見圖2),其共有14片葉片,直徑 為60mm,高度為18mm。葉片厚度為1mm,葉片間距最小為1mm。葉輪材料為7A04。
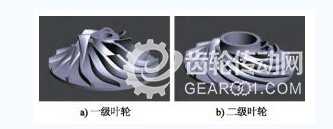
圖2 某葉輪系列模型
由于受體積限制,葉輪采用小直徑、大扭角的結構,這給葉片的加工帶來了更高的難度:整體葉輪加工流道窄,葉片相對長,葉片間距最小處≤1.5mm,一般需要采用小刀具直徑加工,加工過程中易造成刀具斷裂。
3.2 刀具切削參數的選用
選用SECO 的極 小 徑 系 列 刀 具,選 用4和2mm 刀具進行粗加工;1.2mm 刀具進行半精加工留余量0.1mm;1mm 刀具 進 行 精 加 工。精 加 工刀具為錐桿結構,切削刃末端為縮頸,該結構在讓開干涉的同時最大限度地提高了刀具強度,保證了加工穩 定 性。刀 柄 采 用 HSK——A63 熱脹 刀 柄 夾 持。切削參數見表3。
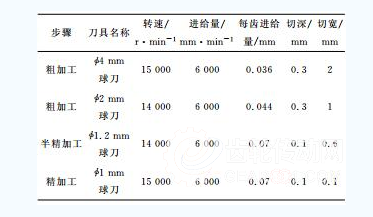
表3 切削參數
3.3 走刀過程
本次加工使用 CATIA 軟件編制加工程序。粗加工采用插銑加工方法,刀具沿葉片各角度的切線方向對葉輪進行插銑加工。插銑粗加工的優點如下:1)由于切削力為軸向力,可采用大懸伸避免干涉;2)可減小工件變形;3)提高加工效率。粗加工插銑采用 定 軸3+2方式 進 行 分 層 加 工(見 圖 3)。在 CATIA 軟件中 選 擇 等 高 降 層 粗 銑 策 略,以 流 道輪廓為限制線,兩側葉頂為干涉面,刀軸方向以一次策略為單位多次旋轉,以達到讓開干涉,去除大余量的目的。
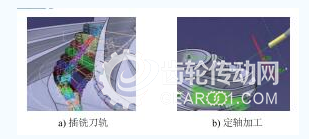
圖3 粗加工示意圖
精加工中,流道底部按照3個區域分別拾取加工面,使用曲面等參數線加工策略,選擇插補軸的多軸方式,以區域邊界多個驅動軸為刀軸方向,通過手動設置適應 曲 率 變 化,形 成 整 齊、穩定和高效的刀路。主葉片吸力面、主葉片壓力面、分流葉片吸力面和分流葉片壓力面分別采用同樣的策略,以無干涉、無跳刀和加工完整為目的,以區域邊界的25個驅動軸為刀軸方向,通過手動設置來適應劇烈的曲率變化,生成整齊可靠的刀路(見圖4)。
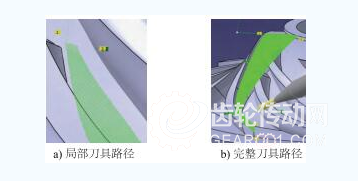
圖4 精加工示意圖
4、 結語
高速切削已經在航空領域得到廣泛應用,本文從刀具結構、刀具幾何參數、刀具夾持系統以及加工工藝等影響因素進行分析,并結合航空殼體零件在實際加工中的應用實例,進一步掌握刀具在高速切削中的影響,從而提升高速切削的應用效果,降低加工成本。
柄、機床、控制系統和加工工藝等方面均與常規加工有很大區別。由于不同的加工方式、不同的工件材料有不同的高速切削范圍,因而應根據不同的加工材料,結 合 實 際 生 產 情 況,確 定 合 理 的 高 速 切 削 范圍[2——6]。高速切削的速度范圍與被加工材料的關系如圖1所示。