在設(shè)計(jì)開發(fā)六檔轎車變速器時(shí),最大輸入扭矩增加到180Nm以上,為了減少變速器重量,結(jié)構(gòu)更加輕便,僅采用滲碳淬火工藝已無(wú)法滿足齒輪疲勞壽命的設(shè)計(jì)要求。為此,我司從材料、工藝上進(jìn)行新的嘗試來(lái)提升齒輪根部的彎曲疲勞強(qiáng)度和齒輪表面的接觸疲勞強(qiáng)度。而影響疲勞強(qiáng)度的因素有受力狀態(tài)、工作溫度、材料的化學(xué)成分及顯微組織、表面質(zhì)量和殘余應(yīng)力等。現(xiàn)主要考慮合金元素、表面狀態(tài)對(duì)疲勞強(qiáng)度的影響,通過(guò)工藝開發(fā),充分發(fā)掘材料的性能來(lái)提高疲勞強(qiáng)度,滿足疲勞壽命的設(shè)計(jì)要求。
1.增加低碳合金鋼中Ni元素含量
變速器齒輪可采用SAE8620H材料代替20CrMoH來(lái)提高齒輪根部的彎曲疲勞強(qiáng)度,表1為SAE8620H與20CrMoH材料主要化學(xué)成分的區(qū)別。SAE8620H材料Ni元素含量增加了約0.50%,Cr元素含量減少約0.50%,即用0.50%的Ni元素代替0.50%的Cr元素。Ni元素能中等強(qiáng)化鐵素體,增加Ni元素能很好地提高心部鐵素體組織的強(qiáng)度。分別抽取不同爐號(hào)的10個(gè)試樣,進(jìn)行力學(xué)性能試驗(yàn),見表2,SAE8620H試樣屈服強(qiáng)度明顯高于20CrMoH試樣10%以上,有利于齒輪根部彎曲疲勞強(qiáng)度的提升。
表1 20CrMoH與SAE8620H主要化學(xué)成分(質(zhì)量分?jǐn)?shù))要求(%)
表2 20CrMoH和SAE8620H屈服強(qiáng)度對(duì)比
2.控制齒輪淬火后的心部硬度
而Ni元素對(duì)淬透性的影響弱于Cr元素,在其他主要成分相差不大時(shí),SAE8620H的淬透性明顯低于20CrMoH,J9端淬值通常低3HRC左右,即使轎車變速器齒輪模數(shù)≤3mm,但對(duì)心部硬度造成的影響很明顯。為了充分發(fā)揮SAE8620H材料的韌性,提高齒輪根部彎曲疲勞強(qiáng)度,通過(guò)臺(tái)架試驗(yàn)發(fā)現(xiàn)轎車變速器齒輪的心部硬度最佳控制在35~40HRC。SAE8620H材料可以采取如下措施來(lái)提高齒根心部硬度:選取合適的端淬值;適當(dāng)冷速的淬火油;提高淬火溫度;提高淬火時(shí)冷卻烈度及均勻性等。
3.選取合適的噴丸強(qiáng)化工藝
對(duì)扭矩要求更高的齒輪副,在齒部精加工后增加強(qiáng)力噴丸工藝,在齒輪表層形成一塑性變形層即強(qiáng)化層,當(dāng)前我司噴丸強(qiáng)化工藝強(qiáng)化層深度約為0.15mm。利用該表面塑性變形層分別從殘余壓應(yīng)力場(chǎng)、變形顯微組織、殘留奧氏體向馬氏體轉(zhuǎn)變、機(jī)加工刀痕的有效消除等方面來(lái)改善齒輪的疲勞強(qiáng)度。
但噴丸強(qiáng)化是具有動(dòng)能的高速鋼丸噴打到齒面,使齒部產(chǎn)生塑性變形,對(duì)齒面存在較大的損傷。對(duì)于研磨齒面,粗糙度變差約0.2μm、齒部精度下降一級(jí)以上。通過(guò)選取較低的噴丸強(qiáng)度(弧高值0.2~0.3mmA),配合圓度G2級(jí)以上的切絲鋼丸,能有效減少齒面塑性變形量,而表層殘余壓應(yīng)力又能達(dá)到600MPa以上的設(shè)計(jì)要求。 在正常噴丸強(qiáng)化后,采用直徑0.2mm的切絲鋼丸再進(jìn)行一次更低強(qiáng)度的噴打,能進(jìn)一步優(yōu)化齒面粗糙度,減少表層疲勞微裂紋源。
4.噴丸強(qiáng)化后磷化處理
針對(duì)噴丸強(qiáng)化后齒面損傷問題,可在噴丸強(qiáng)化后再增加錳系抗磨磷化工藝。齒面在噴丸強(qiáng)化過(guò)程中產(chǎn)生了大量的凹坑,磷化膜能很好地覆蓋凹坑,提升齒面粗糙度,同時(shí)磷化膜具有多孔結(jié)構(gòu)可吸附大量潤(rùn)滑油,改善齒面潤(rùn)滑狀況。為了獲得的較好的存油效果,采用90~98℃的高溫磷化工藝,磷化膜厚度10~25μm,磷化膜晶粒度3~16μm,表面腐蝕深度控制在0~4級(jí)。經(jīng)實(shí)驗(yàn)測(cè)量,磷化后齒面摩擦因數(shù)約為0.151,優(yōu)于普通磨齒齒面摩擦因數(shù),改善了齒面嚙合時(shí)潤(rùn)滑狀態(tài),從而延長(zhǎng)了齒輪副疲勞壽命。
5.噴丸強(qiáng)化后高能等離子噴涂處理
(1)表層顯微組織相變強(qiáng)化
高能等離子噴涂工藝致使表層約20μm深度區(qū)域化學(xué)成分及顯微組織發(fā)生改變,從20μm~0.15mm處依然是噴丸強(qiáng)化層。高能等離子噴涂,采用Mo等合金元素組成的復(fù)合材料,鉬能使鋼的晶粒細(xì)化,提高力學(xué)性能。在高溫高壓的條件下撞擊并滲透進(jìn)母材的20μm以內(nèi)深度表面,使金屬表面20μm以內(nèi)深度的晶相組織發(fā)生改變(見圖1、圖2),圖2表面波紋度很小,幾乎沒有晶界氧化,疲勞微裂紋就不易從表面發(fā)生,有利于齒面疲勞強(qiáng)度的提高。
圖1 滲碳淬火后金相組織(500×)
圖2 噴涂后金相組織(500×)
經(jīng)過(guò)高能等離子噴涂后,表面顯微硬度有所提升(見表3),雖影響很淺,但能適當(dāng)提升齒面接觸疲勞強(qiáng)度。
表3 輸入軸噴涂前后表面硬度值
(2)殘余壓應(yīng)力增加
從殘余應(yīng)力檢測(cè)值表4可看出,次表層殘余壓應(yīng)力增加量達(dá)到10%以上,進(jìn)一步強(qiáng)化了壓應(yīng)力場(chǎng),而提升疲勞強(qiáng)度。
表4 輸入軸齒部噴涂前后殘余應(yīng)力值
(3)齒面摩擦因數(shù)的改善
在加工過(guò)程中加入固體潤(rùn)滑劑,固體潤(rùn)滑劑滲入金屬表面后,使表面具有自潤(rùn)滑的效果,摩擦阻力減少。經(jīng)過(guò)摩擦試驗(yàn)測(cè)試(見圖3),干摩擦因數(shù)下降12.1%,濕摩擦因數(shù)下降7.8%,齒輪副在嚙合過(guò)程中,齒面運(yùn)轉(zhuǎn)狀況得到進(jìn)一步改善。
經(jīng)過(guò)高能等離子噴涂后,齒形輪廓偏差、螺旋線輪廓偏差值下降4~6μm;對(duì)于0.8~1.6μm的磨、剃齒面,齒面粗糙度改善約50%(見表5)。高能等離子噴涂能很好地彌補(bǔ)噴丸強(qiáng)化給齒面帶來(lái)的損傷,優(yōu)化齒輪表面質(zhì)量,從而提升疲勞強(qiáng)度。
表5 輸入軸噴涂前后粗糙度變化
6.結(jié)語(yǔ)
綜上所述,提高低碳合金鋼齒輪的疲勞強(qiáng)度,可以采取以下措施:
(1)選取韌性較好的SAE8620H等含Ni低碳合金鋼。
(2)采用合適的滲碳淬火工藝,控制齒輪心部硬度。
(3)采取適當(dāng)?shù)膰娡鑿?qiáng)化工藝,提升表層殘余壓應(yīng)力值。
(4)強(qiáng)噴后增加高溫等離子噴涂等復(fù)合工藝。
1.增加低碳合金鋼中Ni元素含量
變速器齒輪可采用SAE8620H材料代替20CrMoH來(lái)提高齒輪根部的彎曲疲勞強(qiáng)度,表1為SAE8620H與20CrMoH材料主要化學(xué)成分的區(qū)別。SAE8620H材料Ni元素含量增加了約0.50%,Cr元素含量減少約0.50%,即用0.50%的Ni元素代替0.50%的Cr元素。Ni元素能中等強(qiáng)化鐵素體,增加Ni元素能很好地提高心部鐵素體組織的強(qiáng)度。分別抽取不同爐號(hào)的10個(gè)試樣,進(jìn)行力學(xué)性能試驗(yàn),見表2,SAE8620H試樣屈服強(qiáng)度明顯高于20CrMoH試樣10%以上,有利于齒輪根部彎曲疲勞強(qiáng)度的提升。
表1 20CrMoH與SAE8620H主要化學(xué)成分(質(zhì)量分?jǐn)?shù))要求(%)
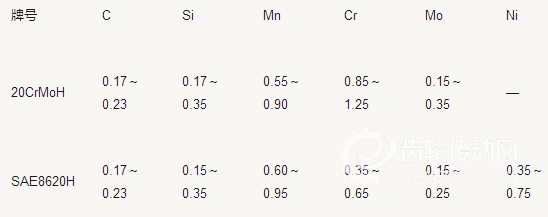
表2 20CrMoH和SAE8620H屈服強(qiáng)度對(duì)比
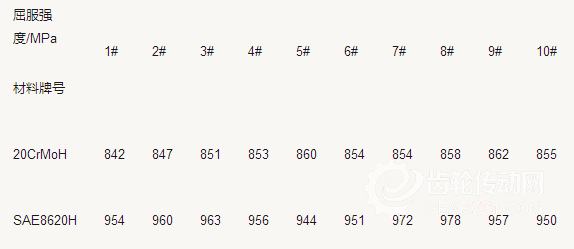
2.控制齒輪淬火后的心部硬度
而Ni元素對(duì)淬透性的影響弱于Cr元素,在其他主要成分相差不大時(shí),SAE8620H的淬透性明顯低于20CrMoH,J9端淬值通常低3HRC左右,即使轎車變速器齒輪模數(shù)≤3mm,但對(duì)心部硬度造成的影響很明顯。為了充分發(fā)揮SAE8620H材料的韌性,提高齒輪根部彎曲疲勞強(qiáng)度,通過(guò)臺(tái)架試驗(yàn)發(fā)現(xiàn)轎車變速器齒輪的心部硬度最佳控制在35~40HRC。SAE8620H材料可以采取如下措施來(lái)提高齒根心部硬度:選取合適的端淬值;適當(dāng)冷速的淬火油;提高淬火溫度;提高淬火時(shí)冷卻烈度及均勻性等。
3.選取合適的噴丸強(qiáng)化工藝
對(duì)扭矩要求更高的齒輪副,在齒部精加工后增加強(qiáng)力噴丸工藝,在齒輪表層形成一塑性變形層即強(qiáng)化層,當(dāng)前我司噴丸強(qiáng)化工藝強(qiáng)化層深度約為0.15mm。利用該表面塑性變形層分別從殘余壓應(yīng)力場(chǎng)、變形顯微組織、殘留奧氏體向馬氏體轉(zhuǎn)變、機(jī)加工刀痕的有效消除等方面來(lái)改善齒輪的疲勞強(qiáng)度。
但噴丸強(qiáng)化是具有動(dòng)能的高速鋼丸噴打到齒面,使齒部產(chǎn)生塑性變形,對(duì)齒面存在較大的損傷。對(duì)于研磨齒面,粗糙度變差約0.2μm、齒部精度下降一級(jí)以上。通過(guò)選取較低的噴丸強(qiáng)度(弧高值0.2~0.3mmA),配合圓度G2級(jí)以上的切絲鋼丸,能有效減少齒面塑性變形量,而表層殘余壓應(yīng)力又能達(dá)到600MPa以上的設(shè)計(jì)要求。 在正常噴丸強(qiáng)化后,采用直徑0.2mm的切絲鋼丸再進(jìn)行一次更低強(qiáng)度的噴打,能進(jìn)一步優(yōu)化齒面粗糙度,減少表層疲勞微裂紋源。
4.噴丸強(qiáng)化后磷化處理
針對(duì)噴丸強(qiáng)化后齒面損傷問題,可在噴丸強(qiáng)化后再增加錳系抗磨磷化工藝。齒面在噴丸強(qiáng)化過(guò)程中產(chǎn)生了大量的凹坑,磷化膜能很好地覆蓋凹坑,提升齒面粗糙度,同時(shí)磷化膜具有多孔結(jié)構(gòu)可吸附大量潤(rùn)滑油,改善齒面潤(rùn)滑狀況。為了獲得的較好的存油效果,采用90~98℃的高溫磷化工藝,磷化膜厚度10~25μm,磷化膜晶粒度3~16μm,表面腐蝕深度控制在0~4級(jí)。經(jīng)實(shí)驗(yàn)測(cè)量,磷化后齒面摩擦因數(shù)約為0.151,優(yōu)于普通磨齒齒面摩擦因數(shù),改善了齒面嚙合時(shí)潤(rùn)滑狀態(tài),從而延長(zhǎng)了齒輪副疲勞壽命。
5.噴丸強(qiáng)化后高能等離子噴涂處理
(1)表層顯微組織相變強(qiáng)化
高能等離子噴涂工藝致使表層約20μm深度區(qū)域化學(xué)成分及顯微組織發(fā)生改變,從20μm~0.15mm處依然是噴丸強(qiáng)化層。高能等離子噴涂,采用Mo等合金元素組成的復(fù)合材料,鉬能使鋼的晶粒細(xì)化,提高力學(xué)性能。在高溫高壓的條件下撞擊并滲透進(jìn)母材的20μm以內(nèi)深度表面,使金屬表面20μm以內(nèi)深度的晶相組織發(fā)生改變(見圖1、圖2),圖2表面波紋度很小,幾乎沒有晶界氧化,疲勞微裂紋就不易從表面發(fā)生,有利于齒面疲勞強(qiáng)度的提高。
圖1 滲碳淬火后金相組織(500×)
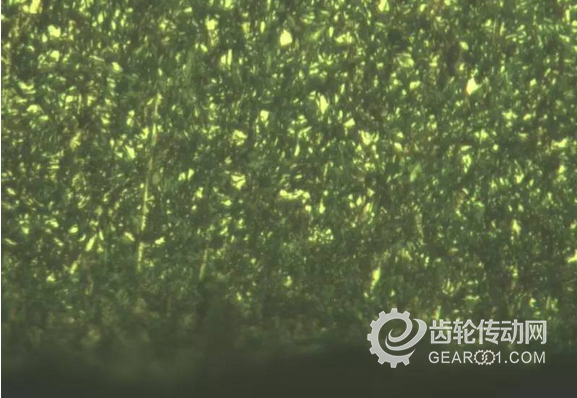
圖2 噴涂后金相組織(500×)
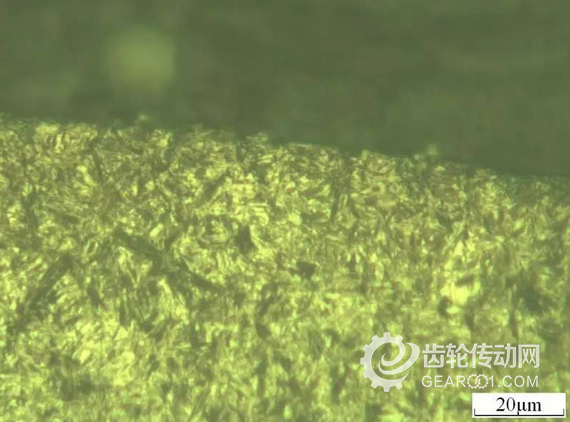
經(jīng)過(guò)高能等離子噴涂后,表面顯微硬度有所提升(見表3),雖影響很淺,但能適當(dāng)提升齒面接觸疲勞強(qiáng)度。
表3 輸入軸噴涂前后表面硬度值
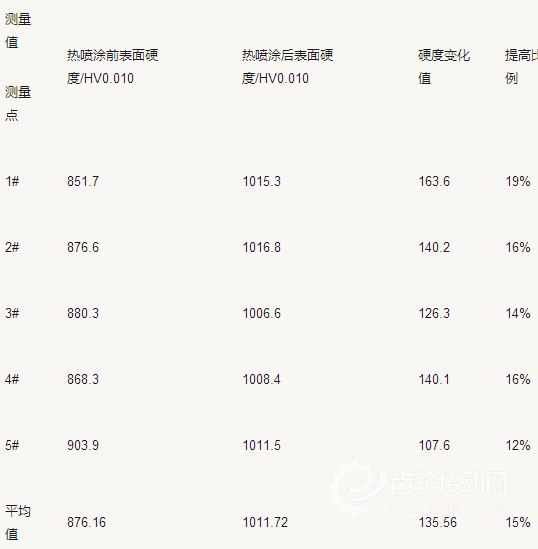
(2)殘余壓應(yīng)力增加
從殘余應(yīng)力檢測(cè)值表4可看出,次表層殘余壓應(yīng)力增加量達(dá)到10%以上,進(jìn)一步強(qiáng)化了壓應(yīng)力場(chǎng),而提升疲勞強(qiáng)度。
表4 輸入軸齒部噴涂前后殘余應(yīng)力值
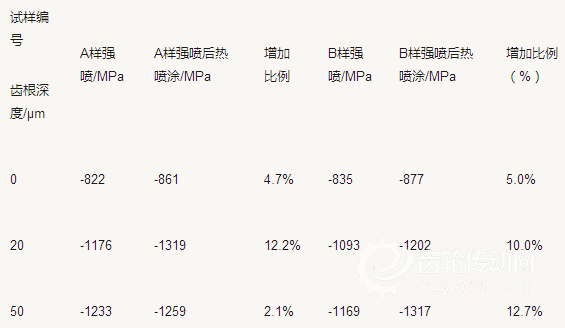
(3)齒面摩擦因數(shù)的改善
在加工過(guò)程中加入固體潤(rùn)滑劑,固體潤(rùn)滑劑滲入金屬表面后,使表面具有自潤(rùn)滑的效果,摩擦阻力減少。經(jīng)過(guò)摩擦試驗(yàn)測(cè)試(見圖3),干摩擦因數(shù)下降12.1%,濕摩擦因數(shù)下降7.8%,齒輪副在嚙合過(guò)程中,齒面運(yùn)轉(zhuǎn)狀況得到進(jìn)一步改善。
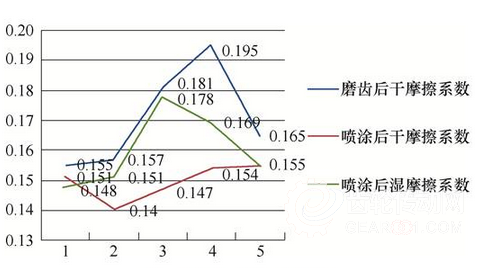
經(jīng)過(guò)高能等離子噴涂后,齒形輪廓偏差、螺旋線輪廓偏差值下降4~6μm;對(duì)于0.8~1.6μm的磨、剃齒面,齒面粗糙度改善約50%(見表5)。高能等離子噴涂能很好地彌補(bǔ)噴丸強(qiáng)化給齒面帶來(lái)的損傷,優(yōu)化齒輪表面質(zhì)量,從而提升疲勞強(qiáng)度。
表5 輸入軸噴涂前后粗糙度變化
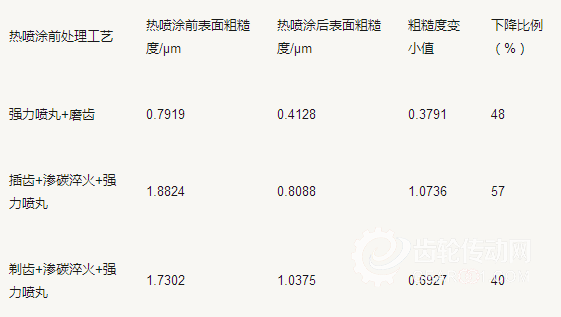
綜上所述,提高低碳合金鋼齒輪的疲勞強(qiáng)度,可以采取以下措施:
(1)選取韌性較好的SAE8620H等含Ni低碳合金鋼。
(2)采用合適的滲碳淬火工藝,控制齒輪心部硬度。
(3)采取適當(dāng)?shù)膰娡鑿?qiáng)化工藝,提升表層殘余壓應(yīng)力值。
(4)強(qiáng)噴后增加高溫等離子噴涂等復(fù)合工藝。