離子滲氮是利用稀薄氣體(滲劑)在強電場的作用下,將含氮氣體滲劑電離成氮離子,氮離子在電場的作用下高速向工件表面運動,通過濺射沉積作用在工件表面形成一定厚度的滲氮層。與其他滲氮方式相比,離子滲氮由于滲速快、滲層相成分易控制、節能環保等優勢,被廣泛應用到齒輪的表面改性上。但也由于輝光存在一定厚度,在深孔或窄縫中無法提供產生輝光厚度的空間,導致滲氮困難甚至無法滲氮;另外,在一定尺寸的小孔與窄縫處易產生輝光疊加,造成工件加熱溫度不均勻,從而使滲層厚度和硬度不均勻,以致出現熱處理不合格。
齒輪是傳遞動力的關鍵部件,在傳遞動力過程中承受摩擦、沖擊、剪切等應力,因此要求齒面具有高的耐磨、抗咬合等性能。齒輪常見的失效形式是齒面出現麻點、接觸疲勞破壞及滲層剝落、齒根處斷裂等,其中以沿齒根斷裂危害性最大。中碳合金鋼齒輪經調質后進行滲氮處理,可使齒面硬度提高到 500 ~ 1200 HV,有效提高齒面的耐磨性和抗咬合性能。同時,滲氮層在表面形成壓應力,提高齒根處疲勞強度,使得齒輪壽命大大延長。
由于齒輪的特殊形狀和輝光離子滲氮的特性,如果滲氮工藝參數控制不當,在近齒根處易出現滲層深度不夠,甚至無滲氮現象,導致齒根處強化效果達不到要求。目前,針對這種情況熱處理廠均都沒有很好的應對措施,只知道齒輪離子滲氮應采用較大爐壓,以減小輝光厚度,使得齒輪根部能充分滲氮,但對應模數大小與工況的齒輪適用多高爐壓,還沒有資料參考。為了提高檢測效率和降低檢測成本,絕大多數熱處理廠家采用簡單的圓形或方形試樣檢測齒輪離子滲氮的滲氮質量,這時往往會出現試樣滲氮檢測合格而齒輪不合格現象。即使個別廠家隨工件配置同形狀和狀態的齒形試樣,當試樣檢測不合格時也只是調整工藝進行補滲,多次滲氮又會導致變形量大幅增加,降低齒輪精度,同時嚴重浪費能源和延長工期。本研究選擇模數 4 mm 的小齒輪對其在不同爐壓下進行離子滲氮試驗,以供生產參考。
一、試驗材料與方法
試驗材料為齒輪最常用 42CrMo 鋼,化學成分(質量分數,% )為 0. 39 ~ 0. 42C、0. 16 ~ 0. 24Mo、0. 75 ~ 1. 0Mn、0. 15 ~ 0. 34Si、0. 9 ~ 1. 02Cr,余量 Fe。調質工藝為 850 ℃ × 1 h 油淬 + 560 ℃ × 3 h 回火,調質硬度 為 280 ~ 300 HBW。從齒輪本體上取樣,取樣齒輪具體參數見表 1。
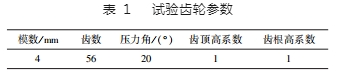
試驗設備采用某研究所生產的單熱源脈沖式離子滲氮爐,爐壓為 180、230、280 和 330 Pa。滲氮過程為抽真空→打弧→通氬氣升溫→到溫后通氨氣,通入量為 0.5 L / min,調整氬氣通入量達到設定爐壓進行滲氮,具體工藝見表 2。
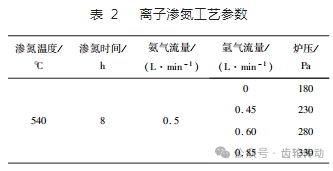
根據 GB / T 11354—2005《鋼鐵零件滲氮層深度測定和金相組織檢驗》采用硬度法對試樣齒頂、節圓、齒根處滲氮層深度進行測量,測量位置見圖 1。用小負荷顯微硬度計從表面 0.1mm 處向心部每隔 0.05mm 測試一個硬度值(加載載荷砝碼為 300g,加載時間為 15s),見圖 2,以比基體高 50 HV 的位置作為滲層深度。用金相顯微鏡對滲層組織進行判定。
二、試驗結果
滲氮層深度
齒輪節圓處是受摩擦力最大的地方,該處滲層硬度越高、滲層越深其耐磨性能越好。當齒輪在傳遞動力過程中,由于齒根處受到循環應力作用,所以在齒根處易出現疲勞斷裂。齒輪滲氮會在表面形成壓應力,滲層越深,壓應力越大;表面壓應力越大,越有利于疲勞性能的改善。所以評判一個齒輪的滲氮質量,需對齒輪節圓和齒根的滲氮層硬度、深度和組織進行測量和評級。
滲層深度測試結果見表 3。由表 3 可以看出,當爐內壓強為 180 Pa 時,從齒頂到節圓處滲層深度從 0.23 mm減小到 0.15 mm,在節圓偏下(偏齒根處)滲層深度即接近于零。保持氨氣流量不變,向爐內通入氬氣,當爐壓增加到 230 Pa,齒頂滲層深度稍有增加,節圓處滲層深度達到 0.23 mm,此時齒根處滲層深度為 0.15 mm,與節圓、齒頂的滲層深度相比,仍有較大差距。保持氨氣通入量不變,繼續增加氬氣通入量,使爐壓升高到 280 Pa,此時齒頂、節圓和齒根滲層深度分別達到 0.32、0.33 和 0.24 mm,滲層深度從齒頂到齒根處全部增加,雖然齒頂到齒根的滲層深度仍存在梯度,但滲層的均勻性得到較大改善。繼續增加氬氣通入量,使爐壓升高到 330 Pa,此時齒頂、節圓、齒根滲層深度分別達到 0.35、0.34 和 0.28 mm,滲層深度和均勻性進一步得到改善。但此時由于輝光厚度較薄,爐內放置的輔助卡具間的小縫偶爾出現打弧現象。
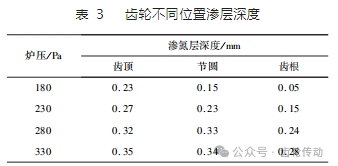
滲氮層硬度梯度
硬度梯度是衡量滲層質量的重要指標之一。當表面硬度相同時,硬度梯度越平緩,越有利于滲層性能的提高。圖 3 為不同爐壓下齒頂、節圓、齒根處滲氮層硬度分布曲線。從圖 3(a)中可以看到,當爐壓為 180 Pa 時,齒頂表面硬度為 648 HV0. 3,為正常的滲氮硬度。而在節圓處表面硬度僅為 527 HV0.3,距表面 0.1 mm 處,硬度僅有 409 HV0.3 左右,表面硬度太低和滲層深度太薄將導致齒輪在使用過程中出現開裂、脫落等現象,嚴重影響滲氮層的耐磨性能。在齒根距表面0.1 mm處硬度和基體硬度無明顯差別。由此可見,模數 4 mm 的齒輪在 180 Pa 爐壓下輪齒滲層非常不均勻。
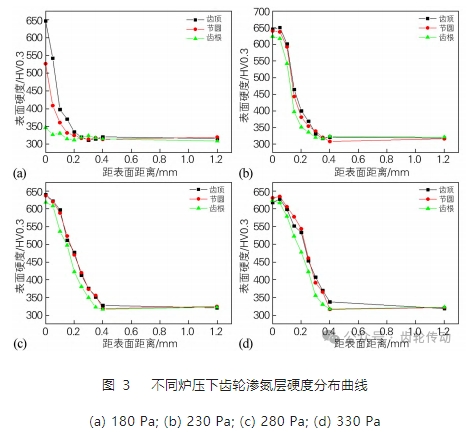
圖 3(b) 為爐壓 230 Pa 時輪齒的滲氮情況,可以看出,齒頂和節圓表面硬度分別為 647 HV0.3 和 638 HV0.3 ,距表面0.1 mm 處硬度可以達到651 HV0.3 和 633 HV0.3,同位置節圓處比齒頂處稍低,但齒根距表面 0.1 mm 處只有 545 HV0.3,與齒頂與節圓處仍有較大差距。圖3(c)為爐壓 280 Pa 時輪齒的滲氮情況,可以看到,齒頂和節圓距表面 0.1 mm 處硬度均可以達到 625 HV0.3 左右,而齒根同位置達到了 610 HV0.3 左右,整個輪齒的滲層深度較均勻,也大大降低了齒根處的硬度梯度。圖 3(d)為爐壓 330 Pa 時輪齒的滲氮情況,可以看到,齒頂和節圓距表面 0.1 mm 處硬度均可以達到 630 HV0.3 左右,而齒根同位置達到了 620 HV0.3 左右,整個輪齒的滲層深度非常均勻。
顯微組織
滲氮層是由化合物層(白亮層)與擴散層組成,化合物層硬且脆,耐腐蝕性最強。滲氮層中化合物層與擴散層的厚度、表面疏松、擴散層中脈狀氮化物的級別都是直接決定滲氮層性能關鍵因素,需通過對滲氮層的顯微組織進行檢驗,對疏松與脈狀氮化物進行評級。圖 4 為輪齒不同部位在不同滲氮條件下齒輪的顯微組織。
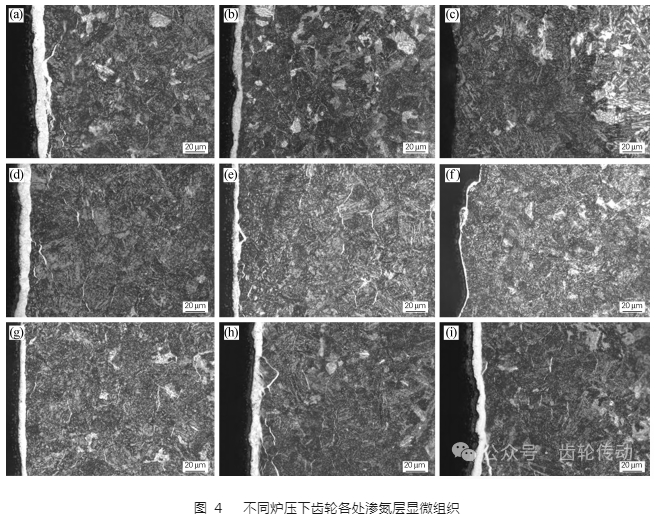
圖 4(a~c)為爐壓為 230 Pa 時,輪齒各處的滲氮層顯微組織??梢钥吹?,在齒頂處有較厚的白亮層,約 10 μm,在節圓處白亮層大幅度減少至 5 μm 左右,而在齒根處幾乎看不到任何白亮層。齒頂、節圓處的化合物層中疏松級別皆為 1 級;而在齒頂處出現了約為 2 級的脈狀氮化物,節圓處和齒根處脈狀氮化物皆為 1 級。
圖 4(d~f)為爐壓為 280 Pa 時,輪齒各處的滲氮層顯微組織??梢钥吹?,在齒頂處的白亮層約 10 μm,在節圓處白亮層厚度和 230 Pa 時相比,沒有明顯變化,而在齒根處出現了為 2 ~ 3 μm 的白亮層。齒頂、節圓、齒根處的化合物層中疏松級別皆為 1 級;而在齒頂和節圓處皆出現了約為 2 級的脈狀氮化物,齒根處脈狀氮化物為 1 級。
圖 4(g~i)為爐壓為 330 Pa 時,輪齒各處的滲氮層顯微組織??梢钥吹剑邶X頂處的白亮層和 230 Pa 和 280 Pa 時相比,稍有減薄,約為 7 μm,在節圓和齒根處白亮層厚度和 230 Pa 和 280 Pa 時相比,明顯增加,約為 8 μm。齒頂、節圓、齒根處的化合物層中疏松級別皆為 1 級;在齒頂和節圓處脈狀氮化物約為 2 級,且在齒根處也出現了微量的脈狀氮化物。
化合物層硬且脆,具有較高的耐蝕性能和較低的摩擦因數,較厚的化合物層可有效提高滲氮層的耐蝕性能、耐磨性和抗膠合性能,卻對抗疲勞性能不利;所以對模數為 4 mm 的齒輪離子滲氮時,可選擇適當的工藝,保證節圓處的化合物層厚度,而減小齒根處的化合物層厚度。
三、結果分析
離子滲氮由于滲速快、相成分可控和環保節能等一系列優點,被大量用于改善齒輪表面耐磨性、抗咬合及抗疲勞等性能上。但由于其滲層淺、硬度梯度較陡,一般用于模數 4 mm 以下齒輪的表面改性上。而齒輪模數越小,齒槽的寬度越小,特別是節圓到齒根部分,形成的縫隙越窄。
離子滲氮產生的輝光具有一定厚度 d(2 ~ 8 mm),當窄縫或小孔尺寸小于 2d 時,無法為正常產生輝光提供足夠的空間,故無法正常滲氮,也就無法得到工況所需的滲氮層厚度和組織。輝光厚度和離子滲氮爐內的壓強成反比:爐壓越高,輝光厚度越薄。
模數 4 mm 的齒輪在節圓處兩齒之間的寬度約為 5 mm,而爐壓為 180 Pa 時,輝光厚度約為 4 mm,此時兩相鄰輪齒之間的距離從節圓至齒根部都將無法給輝光提供足夠空間,致使滲氮無法正常進行,距離越小滲氮越困難,所以本文試驗齒輪從節圓到齒根部,滲層逐漸減少。
保持向離子滲氮爐內通入的氨氣量不變,向爐內通入氬氣,致使爐內壓強增加,輝光厚度變薄,在更小的空間內能進行正常滲氮,所以從齒頂到齒根滲氮層深度差逐漸減小。本文中當爐壓為 230 Pa 時,模數為 4 mm 的小齒輪試樣齒根部滲層深度已是節圓處的 65% 左右;當爐壓升高到 280 Pa 時,齒根部滲層深度升至節圓處的 73% 左右;當爐壓升高到 330 Pa 時,齒根部滲層深度升至節圓處的 82% 左右。
氬離子相比于氫離子和氮離子,具有較強的轟擊強度。根據濺射沉積理論可知,首先,轟擊強度越強,從試樣(工件)表面轟擊出的鐵和合金離子越多,在試樣表面產生合金氮化物越多,強化了濺射沉積作用,導致試樣表面氮勢升高,增加了擴散動力;其次,轟擊強度越強,作用在試樣表面上的力越大,產生晶體缺陷越多,越有利于氮元素擴散。最后,根據文獻的研究成果,經過氬氣 4 h 離子濺射激活處理,再經 550 ℃ × 6 h 離子滲氮處理后,表面 γ′相從 55% 降低到 45% ,表面 α 相從 25% 增加到 42% ,ε 相從 20% 降低到 13% ,可見離子濺射激活處理的試樣,滲氮時表面化合物層中 α 相數量增加,ε 相減少,形成以 γ′相為主和夾雜著 α 相的化合物層,有利于次表層氮的擴散,加速了擴散層的形成。
據此,解釋了本文隨著氬氣通入量的增加,化合物層的厚度微量減薄的原因。所以在離子滲氮氣氛中加入適量的氬氣,不僅有利于加快滲氮速率,同時可以減少化合物層厚度。在本試驗中,隨著氬氣通入量的增加滲速逐漸增加,但爐壓增加到 330 Pa 時,由于輝光厚度此時約 2 mm,致使爐內卡具之間的部分縫隙產生輝光疊加,局部出現溫度超高的情況。在實際生產中,由于裝爐量更大,情況更復雜,當輝光太薄時,許多窄縫、小孔容易產生輝光疊加,造成局部溫度超高或者打弧現象,使得產品報廢,所以使用 330 Pa 爐壓進行離子滲氮時需謹慎。
四、結論
1)對齒輪進行離子滲氮時要嚴格控制爐內壓強,壓強越大,輪齒滲氮層越均勻。
2)齒輪離子滲氮過程中保持氨氣通入量不變的同時加入適量的氬氣,可以有效減小輝光厚度。
3)對模數4 mm 的齒輪經540 ℃ × 8 h 離子滲氮,其滲層均勻性隨著氬氣通入量的增加逐漸改善。當爐壓低于 180 Pa 時,齒根處無法滲氮;當爐壓高于 280 Pa 時,爐內由于輝光厚度太薄,打弧幾率增加,爐溫均勻性變差。
4)在氨氣中通入氬氣可增加離子轟擊效果,減少化合物層厚度和在一定程度上提高滲氮速率,但爐壓對滲層疏松和脈狀氮化物級別無明顯影響。
參考文獻略.