近年來,隨著全球經(jīng)濟快速發(fā)展與基礎設施建設投入增加,城市化水平不斷提高,隧道及地下空間開發(fā)快速發(fā)展,盾構(gòu)機設備在國內(nèi)外得到廣泛應用,產(chǎn)品需求與日劇增。隨著盾構(gòu)機設備生產(chǎn)交付周期縮短,產(chǎn)品質(zhì)量要求提高,對產(chǎn)品工藝方案的高效性、安全性提出了更高的要求。
《中國制造 2025》指出,在重點領(lǐng)域推進一批智能工廠和數(shù)字化工廠建設,重點推進生產(chǎn)過程的數(shù)字化、網(wǎng)絡化和智能化,推進我國制造業(yè)加速向智能制造轉(zhuǎn)變。裝配自動化和信息化是實現(xiàn)智能制造規(guī)劃不可或缺的部分,也是提升產(chǎn)品質(zhì)量和競爭力的重要手段。主驅(qū)動作為盾構(gòu)機最核心部件,因其裝配工藝流程復雜、質(zhì)量管控點多和裝配技術(shù)要求高等特點一直以來都是盾構(gòu)機制造過程中的難點,其裝配自動化、信息化建設需求尤為突出。
現(xiàn)階段國內(nèi)外盾構(gòu)機的主驅(qū)動裝配工序基本采用集中固定工位式裝配模式,裝配現(xiàn)場多依賴于純?nèi)斯ぷ鳂I(yè),裝配輔助及自動化裝置、信息化管控措施不完善。這種傳統(tǒng)裝配方式主要存在以下問題: 1)裝配效率低,其中以零/ 部件清洗作業(yè)及小齒輪組件的加熱、壓裝作業(yè)為代表,工人勞動強度大,產(chǎn)品產(chǎn)出量有限;2)物料轉(zhuǎn)運效率低,采用叉車轉(zhuǎn)運、行車吊裝的方式進行,生產(chǎn)高峰期叉車和行車資源緊張,耽 誤工期;3)信息化程度低,緊固件擰緊信息及產(chǎn)品裝配進程或異常無法自動記錄和實時傳遞,產(chǎn)品質(zhì)量可追溯性差。
為解決主驅(qū)動裝配中以人工作業(yè)為主的傳統(tǒng)裝配方式帶來的諸多問題,通過對主驅(qū)動零件組成及裝配工序進行分析,合理規(guī)劃裝配工藝流程及生產(chǎn)線布局,建設全新主驅(qū)動裝配生產(chǎn)線,定制開發(fā)和引入專用裝配裝備,重點突破零/ 部件自動化清洗、物料自動化轉(zhuǎn)運、小齒輪組件自動化裝配、緊固件扭矩檢測及裝配質(zhì)量信息可追溯等瓶頸工序。同時通過設計主驅(qū)動裝配生產(chǎn)線智能調(diào)度系統(tǒng),實現(xiàn)主驅(qū)動裝配生產(chǎn)線與上下游產(chǎn)品生命周期管理(Product Lifecycle Management, PLM)、企業(yè)資源計劃(Enterprise Resource Planning, ERP)和數(shù)據(jù)采集與監(jiān)視控制(Supervisory Control And Data Acquisition,SCADA)等系統(tǒng)的互聯(lián)互通,完成生產(chǎn)線各工序之間的信息銜接及設備數(shù)據(jù)采集與監(jiān)控,達到盾構(gòu)機主驅(qū)動裝配質(zhì)量及效率提升的要求。
一、主驅(qū)動裝配需求分析
盾構(gòu)機主驅(qū)動的裝配需求分析是裝配生產(chǎn)線設計的基礎。常規(guī)土壓平衡盾構(gòu)機主驅(qū)動結(jié)構(gòu)主要包括主軸承、變速箱、主驅(qū)動環(huán)件、密封件、減速機、小齒輪和變頻電機等部件。主軸承是主驅(qū)動的核心部件,同時承受軸向、徑向及傾覆力矩;變速箱及主驅(qū)動環(huán)件是主驅(qū)動主體構(gòu)成部分;小齒輪與主軸承大齒圈組成齒輪副以傳遞扭矩。
盾構(gòu)機主驅(qū)動裝配工藝流程如圖 1 所示。根據(jù)主驅(qū)動的裝配工藝需求,結(jié)合各工序的工藝特點和操作的便捷性,裝配生產(chǎn)線主要集成了移動式激光清洗設備、小件清洗專機、轉(zhuǎn)運車(Automatic Guided Vehicle, AGV)、小齒輪組件裝配生產(chǎn)線、工位起重機和扭矩工作站等自動化設備,將整條裝配生產(chǎn)線劃分為卸貨及分揀區(qū)、零/ 部件清洗區(qū)、小齒輪組件裝配區(qū)、物料流轉(zhuǎn)區(qū)及主驅(qū)動總裝區(qū)等,實現(xiàn)了零件清洗自動化、部件裝配規(guī)范化和擰緊信息可追溯。考慮到各工序生產(chǎn)節(jié)拍及流轉(zhuǎn)速度的調(diào)整需求,在工位之間設計合理的緩存區(qū)。針對裝配過程可能產(chǎn)生的不合格品,在裝配生產(chǎn)線設計不合格品存放區(qū),以便根據(jù)產(chǎn)品質(zhì)檢結(jié)果完成后續(xù)處理。
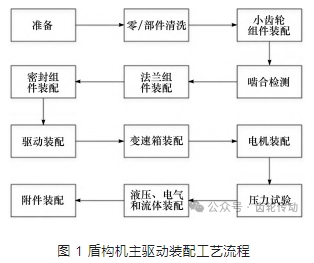
二、主驅(qū)動裝配生產(chǎn)線設計
裝配生產(chǎn)線工藝流程
盾構(gòu)機主驅(qū)動裝配生產(chǎn)線整體設計思路以主驅(qū)動裝配物料流轉(zhuǎn)工藝流程為基礎來規(guī)劃各功能區(qū)域。盾構(gòu)機主驅(qū)動裝配生產(chǎn)線工位布局和物料流轉(zhuǎn)路線分別如圖 2 和圖 3 所示。圖 2 中和圖 3 中,在廠房入口來料卸貨區(qū)卸下物料,依次分揀到小件分揀區(qū)和大件來料緩存區(qū);小件、大型環(huán)件分別利用小件清洗專機、移動式激光清洗機完成自動清洗,將清洗后的零/ 部件轉(zhuǎn)運至相應緩存區(qū);小齒輪組件通過小齒輪組件裝配專機自動完成小齒輪與滾動軸承的加熱與壓裝, 外密封環(huán)在對應緩存區(qū)完成壓力試驗,隨后在總裝工位利用工位起重機及行車完成法蘭、主部件、密封件、驅(qū)動及附件裝配以及嚙合檢測、壓力試驗等工序;在總裝翻身工位可進行環(huán)件及總體翻身,主驅(qū)動裝配完成后根據(jù)質(zhì)檢結(jié)果轉(zhuǎn)運至成品存放區(qū)或不合格品存放區(qū);其中 AGV 負責零/ 部件的靈活流轉(zhuǎn),扭矩管理系統(tǒng)負責緊固件的擰緊、檢測及數(shù)據(jù)傳輸。
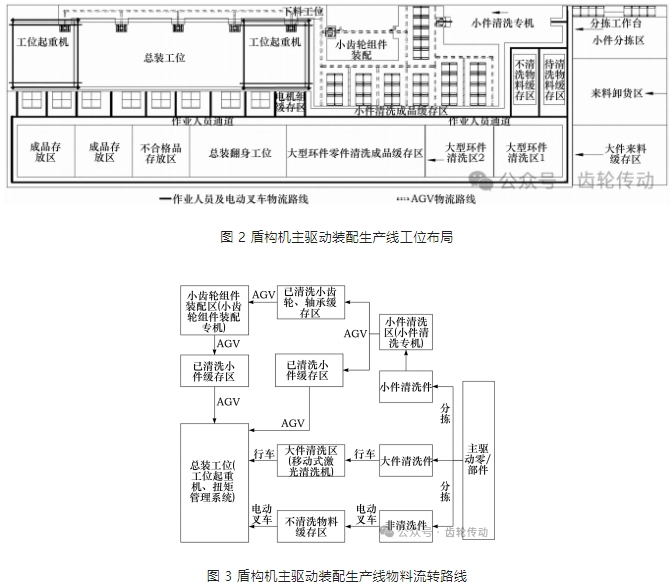
主驅(qū)動零件自動化清洗技術(shù)
根據(jù)主驅(qū)動零/ 部件的結(jié)構(gòu)特點及其清潔度要求,結(jié)合國內(nèi)外先進清洗技術(shù)和設備發(fā)展現(xiàn)狀,應用超聲波清洗、激光清洗等技術(shù),進行不同類型、不同規(guī)格尺寸的主驅(qū)動零/ 部件清洗作業(yè),形成柔性清洗生 產(chǎn)線,提高零/ 部件清洗質(zhì)量和效率,降低人工清洗作業(yè)強度,減少因清潔度未達標導致的返工作業(yè)。
針對主驅(qū)動小齒輪、調(diào)心軸承、軸承套、內(nèi)外壓緊環(huán)、螺栓、螺柱和螺母等小型精密零 / 部件,利用超聲波清洗技術(shù)清除表面輕微銹蝕和油污。所采用的小件清洗專機主要由桁架機構(gòu)、機體、水箱、輸送系統(tǒng)、超聲清洗系統(tǒng)、旋轉(zhuǎn)漂洗系統(tǒng)、旋轉(zhuǎn)吹干系統(tǒng)、熱風烘干系統(tǒng)、液體過濾系統(tǒng)、排污系統(tǒng)、霧氣處理系統(tǒng)及電氣控制系統(tǒng)等組成。通過桁架機構(gòu)實現(xiàn)物料框的自動校正定位及抓取轉(zhuǎn)移,通過電氣控制系統(tǒng)保證設備正常工作,通過三級過濾超聲清洗系統(tǒng)保證清洗精度,通過旋轉(zhuǎn)吹干系統(tǒng)及熱風烘干系統(tǒng)實現(xiàn)工件的快速干燥,多種系統(tǒng)的融合最終實現(xiàn)零/ 部件的自動高效清洗。
小件清洗專機清洗工藝流程如下:首先通過四爪結(jié)構(gòu)機械手抓取料筐,機械手額定負載為 1 t,抓取精度為±2 mm;當料筐進入上料端后,通過兩側(cè)校正氣缸自動進行校正定位,校正精度為±2 mm;隨后由機動輥道輸送系統(tǒng)將料筐自動傳輸至清洗區(qū),依次經(jīng)過超聲清洗、旋轉(zhuǎn)噴淋漂洗,全方位清洗工件;清洗后的工件由旋轉(zhuǎn)吹干系統(tǒng)及熱風烘干系統(tǒng)去除表面水分,并傳輸至下料端;當接近開關(guān)檢測料框支架上無其余料筐時,機械手將料筐轉(zhuǎn)移至下料位的料框支架上,由 AGV 進入料筐下方取料并轉(zhuǎn)運至緩存區(qū)。
小件清洗專機工作系統(tǒng)由 PLC 控制,對不同類型物料分別編號并設置對應控制程序,當清洗機在上料位讀取料框內(nèi)無線射頻識別(Radio Frequency Identification,RFID)卡信息后,自動匹配清洗程序,實現(xiàn)物料的清洗及吹干,達到單框標準清洗節(jié)拍為 10 分/ 套。
針對主驅(qū)動大型零/ 部件(變速箱、主軸承、法蘭、內(nèi)外密封環(huán)、內(nèi)密封支撐環(huán)和連接環(huán))的焊縫清洗、無損清洗和精確定位清洗等需求,研究開發(fā)激光清洗技術(shù)進行表面清洗。
大件清洗階段所用移動式激光清洗機結(jié)構(gòu)如圖 4 所示。圖 4 的結(jié)構(gòu)主要由激光清洗機主機、激光清洗頭、除塵系統(tǒng)、懸臂吊掛裝置和可移動集成小車等部件組成。通過應用表面力學共振、污物熱膨脹和瞬間氣化原理的清洗技術(shù),將窄脈寬、高功率密度的激光束照射于工件表面,使工件表面的油污、銹蝕和氣割氧化物等發(fā)生瞬間蒸發(fā)或剝離,高速有效地清除鋼材件表面有害雜質(zhì)。作為一種非接觸式清洗方法,激光清洗具有綠色環(huán)保、精準可控和無基材損傷等優(yōu)勢。此外,通過配置移動式集成小車,使激光清洗機能靈活調(diào)整清洗位置,使用方便,占地面積小,清洗效率高。
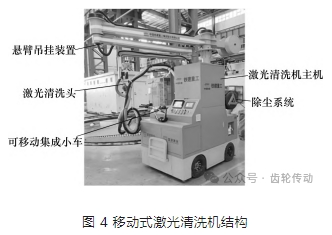
經(jīng)過現(xiàn)場驗證,移動式激光清洗機對主驅(qū)動配件、閥塊和銷軸等精密加工件的表面中等銹蝕、油污, 清理效率可達 40 cm2 / s,對重油污、銹蝕,清理效率 3 ≥ 0 cm2 / s;對于焊縫部位、薄板件表面輕微銹蝕及油污,清理效率可達 40 cm2 / s,對中度銹蝕、油污,清理效率可達 30 cm2 / s,對焊接、涂裝質(zhì)量無任何不良影響。激光清洗后的金屬表面涂裝油漆時涂層附著力≤1 級 (GB / T 9286),涂裝后漆膜表面均勻,無肉眼可見清洗輪廓。
物料自動化轉(zhuǎn)運技術(shù)
在整個裝配生產(chǎn)線工藝流程中,物料的搬運配送是重要組成部分,例如零/ 部件在分揀區(qū)、緩存區(qū)、清洗區(qū)、小齒輪組裝工位及總裝工位等位置的流轉(zhuǎn),物料輸送直接影響到裝配生產(chǎn)線的生產(chǎn)節(jié)拍。針對工位間轉(zhuǎn)運物料的精確性和靈活性要求,本文設計的生產(chǎn)線通過 AGV 來實現(xiàn),具有占地面積小、定位精準和靈活性高的優(yōu)點。
AGV 如圖 5 所示,其采用潛伏舉升式結(jié)構(gòu),搬運物料時升起頂部舉升平臺,背負物料框行走,到達指定地點后舉升平臺下降至低點,將物料框落于支撐架工裝上,AGV 撤離。AGV 通過雙舵輪驅(qū)動轉(zhuǎn)向,可實現(xiàn)前后行走、左右橫移和原地轉(zhuǎn)向動作,以便 AGV 能靈活改變輸送方向。AGV 采用復合導航方式,在裝配生產(chǎn)線上按規(guī)劃路徑行駛時采用激光導航,行走精度小于±10 mm,在庫位中停車采用二維碼導航,停車精 度小于±5 mm,實現(xiàn)精準定位。通過設計輪系懸掛系統(tǒng),使 AGV 適應車間小范圍不平整地面,保證運行時平穩(wěn)無沖擊;此外,為保證運輸過程的安全性,設計了限位裝置,當運行至極限位置時 AGV 能自動停止,同時具備障礙檢測激光雷達、機械防撞、聲光報警和急停等安全防護措施。

在控制系統(tǒng)方面,AGV 以中央控制平臺為基礎, 搭載通信系統(tǒng)、調(diào)度系統(tǒng)及庫位管理系統(tǒng),實現(xiàn)對調(diào)度指令、車輛及交通、地圖路徑數(shù)據(jù)、庫位信息、物料出入庫記錄及庫存信息的綜合管理。為配合小齒輪組件裝配專機完成自動化裝配并保證裝配節(jié)拍,在 AGV 具備一定識別及定位能力的基礎上,重點策劃并匹配物流工藝路線及配送方案,使 AGV 能根據(jù)調(diào)度系統(tǒng)指令自動規(guī)劃物流路徑,執(zhí)行物料框的入庫儲存、出庫運送到目標工位等命令,完成自動配送。
零/ 部件自動化裝配技術(shù)
根據(jù)本裝配生產(chǎn)線總體布局及裝配工藝流程規(guī)劃,將主驅(qū)動零/ 部件裝配分為 2 個部分,首先在小齒輪組件裝配區(qū)利用裝配專機完成相應部件裝配,然后在總裝工位處結(jié)合工位起重機和行車完成剩余步驟的裝配。
小齒輪組件經(jīng)過清洗后轉(zhuǎn)運至小齒輪組件裝配專機工位進行自動加熱及壓裝。小齒輪組件裝配專機如圖 6 所示,主要由桁架式機器人、軸承加熱器、精準定位工作臺和壓裝機協(xié)同開展工作,可實現(xiàn)對軸承及小齒輪的自動上下料、軸承自動加熱保溫、軸承與小齒輪裝配面精準定位、軸承自動壓裝及生產(chǎn)信息展示功能,滿足主驅(qū)動小齒輪組件自動化裝配。通過合理安排各設備工作效率,可保證單套小齒輪組件產(chǎn)出節(jié)拍為 20 分/ 套。
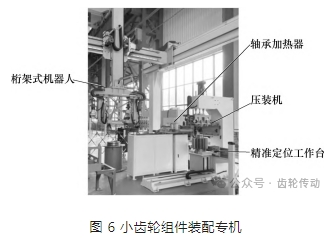
在小齒輪組件裝配專機接收到小齒輪組件裝配指令,同時物料通過 AGV 轉(zhuǎn)運至上料工作位后,自動開始識別檢測、裝配等工作。小齒輪組件裝配工藝流程如圖 7 所示。
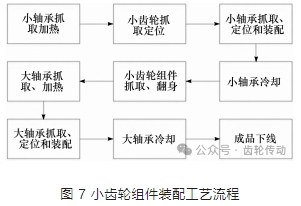
小齒輪組件裝配專機首先通過配備工裝夾具及視覺系統(tǒng)的桁架式機器人自動識別工件的具體型號及裝配工藝尺寸信息,實時分析工件擺放姿態(tài)并選擇合適的抓取角度和抓取位置,實現(xiàn)軸承、小齒輪的抓取及 180°翻身,并按工序要求將零件精準放置在指定工位;抓取工裝末端重復定位精度為±0.5 mm、最大負載為 600 kg。
在軸承加熱階段,通過電磁感應軸承加熱器使軸承在交變磁場產(chǎn)生渦流,從而自動加熱軸承至設定溫度并進行恒溫保溫,軸承加熱器最大承載質(zhì)量為 60 kg,最高加熱溫度可達 120 ℃ ,滿足內(nèi)徑為 Φ80 ~ Φ330 mm、外徑為 Φ150 ~ Φ450 mm 和軸向高度為 46~100 mm 的軸承加熱需求。
在壓裝階段,通過精準定位工作臺,實現(xiàn)軸承內(nèi)圈圓心與小齒輪軸心精準定位,重復定位精度為±0.02 mm;通過壓裝機上的溫度傳感器對軸承內(nèi)圈溫度進行檢測,若軸承內(nèi)圈溫度低于設定值可自動停止壓裝工序,同時將溫度異常的軸承自動返回至軸承加熱器進行二次加熱,直至達到裝配條件方可進行軸承壓裝; 在壓裝過程中通過行程傳感器對軸承軸向壓裝尺寸進行檢測和管控,通過壓力傳感器檢測壓裝狀態(tài),出現(xiàn)異常時及時制動、報警,避免工件損傷;完成壓裝后的小齒輪組件在工作臺上自然冷卻,隨后由桁架機械手將其放至物料托盤上。
在完成小齒輪組件裝配后,將物料轉(zhuǎn)運至總裝工位完成主驅(qū)動其余零/ 部件裝配,此階段起重吊裝主要由工位起重機結(jié)合行車完成。工位起重機結(jié)構(gòu)如圖 8 所示,由主框架、行走軌道(起重機行動軌道)、電動葫蘆、萬向行走腳輪、電動行走腳輪、照明系統(tǒng)和控制系統(tǒng)組成。為滿足主驅(qū)動總裝裝配對作業(yè)空間的要求,設計工位起重機主框架外形尺寸為 9.50m × 9.32m,有效起吊區(qū)域為8.1m×7.1m;為滿足主驅(qū)動大部分小型零/ 部件的起重量及裝配速度需求,在主框架上設計額定負載各為2t 的2根固定軌道和1根行動軌道;采用雙電動行走腳輪加雙萬向行走腳輪結(jié)構(gòu),配置工業(yè)級耐磨腳輪和腳杯,保證工位起重機具備優(yōu)良的調(diào)速和靜動特性;為保證使用安全,配備了安全保護、過載過熱保護、漏電保護及起升限位開關(guān)等保護設施。
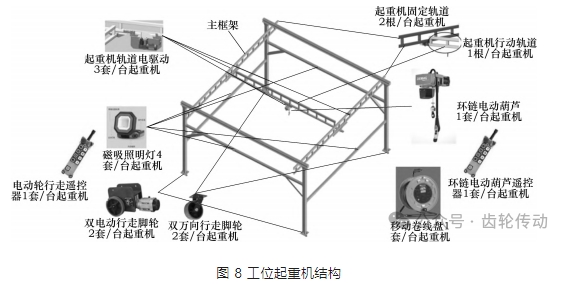
緊固件扭矩管理技術(shù)
在傳統(tǒng)裝配模式下,對于主驅(qū)動部件上的螺栓、螺母等緊固件的扭矩質(zhì)量控制,通常采用自檢與抽檢的人工檢驗手段來實現(xiàn)。在操作過程中,常出現(xiàn)扭矩遺漏、欠扭或過扭及擰緊錯序等問題,給主驅(qū)動的安全平穩(wěn)運轉(zhuǎn)帶來隱患。為提高主驅(qū)動裝配過程中的扭矩管理水平,開發(fā)了一套具備信息記錄與檢測功能的扭矩管理系統(tǒng),其拓撲圖如圖 9 所示。
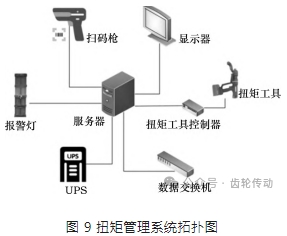
圖 9 中,通過一體式設計,將電動定扭工具(扭矩工具)、反力桿、掃碼槍、套筒選擇器、套筒、平衡器、扭矩工具控制器、不間斷電源(Uninterruptible Power Sys-tem,UPS)和服務器等集成到移動工作小車上,形成移動式扭矩管理工作站;其中,服務器主要負責軟件承載、操作顯示及數(shù)據(jù)匯總,實現(xiàn)了數(shù)據(jù)采集和信號輸入;扭矩工具控制器及扭矩工具用于執(zhí)行扭矩施加作業(yè),能滿足主驅(qū)動使用緊固件(M16 ~ M36) 的裝配空間及扭矩要求,扭矩精度為±6 %;扭矩工具的機身顯示屏可直觀查看扭矩結(jié)果,且能實時與控制器無線網(wǎng)絡通信,保證數(shù)據(jù)穩(wěn)定傳輸;條碼掃碼槍可掃描識別主驅(qū)動零/ 部件信息,報警燈可對擰緊異常項發(fā)出語音及亮燈警報,此外,扭矩管理系統(tǒng)還具備超載、過壓、過流、超溫和防卡死等自動保護功能。
當進行擰緊作業(yè)時,操作工人依次掃描人員碼及部件碼,通過系統(tǒng)數(shù)據(jù)庫識別工號及部件信息后獲取工具操作權(quán),系統(tǒng)將通過事先設定的程序自動將扭矩值和扭矩數(shù)量等信息發(fā)送至相應扭矩工具,操作工人通過顯示終端設備查看裝配工藝文件,選擇合適的扭矩工具及套筒,并按照規(guī)定的裝配順序完成擰緊作業(yè)。系統(tǒng)會實時采集并記錄擰緊階段的扭矩信息,并與預設的程序進行對比,自動檢測擰緊過程是否存在異常,若存在異常,系統(tǒng)將發(fā)出報警提示。同時通過無線網(wǎng)絡將扭矩信息實時傳輸至公司內(nèi)網(wǎng)制造執(zhí)行系統(tǒng)(Manufacturing Execution System,MES),保證數(shù)據(jù)可存儲、分析和追溯。
完成擰緊作業(yè)后,在顯示器上展示作業(yè)人員工號、作業(yè)時間點、工具號、產(chǎn)品和部件號、緊固件位置點位、工具的工作狀態(tài)、擰緊參數(shù)和擰緊結(jié)果判定等追溯所必須的相關(guān)信息。擰緊過程中自動記錄的數(shù)據(jù)上傳至數(shù)據(jù)庫后可進行數(shù)據(jù)分析、生成并進行曲線分析、生成報表、綜合判斷擰緊質(zhì)量情況和擰緊質(zhì)量趨勢等。通過設定不同的報警條件,可將生產(chǎn)事件及時通知推送給指定人員,實現(xiàn)質(zhì)量問題快速響應和高效處理。
信息集成技術(shù)
近年來,生產(chǎn)制造系統(tǒng)逐步朝著信息化、智能化發(fā)展,以便處理海量復雜的生產(chǎn)裝配質(zhì)量信息,進一步提高生產(chǎn)系統(tǒng)的柔性化和自動化水平。為了提高主驅(qū)動裝配過程信息化管理程度,該裝配生產(chǎn)線通 過研發(fā)并設計智能調(diào)度系統(tǒng),實現(xiàn)主驅(qū)動裝配生產(chǎn)線生產(chǎn)計劃與上游 PLM、ERP 等系統(tǒng)的信息銜接,協(xié)同 SCADA 系統(tǒng)完成設備信息及裝配過程的數(shù)據(jù)采集與監(jiān)控,各設備之間的信息交互及裝配過程聯(lián)動信息可通過報表看板展示。盾構(gòu)機主驅(qū)動裝配生產(chǎn)線信息流業(yè)務流程見圖 10。
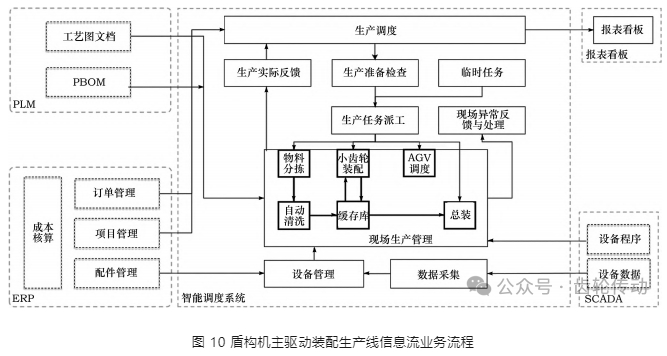
圖 10 中,智能調(diào)度系統(tǒng)負責主驅(qū)動裝配生產(chǎn)線的生產(chǎn)管理,通過對接上游 PLM、ERP 系統(tǒng),接收工藝產(chǎn)品物料清單( Product Bill of Materials,PBOM) 數(shù)據(jù)信息、訂單、項目和配件管理信息,完成生產(chǎn)調(diào)度、計劃派工及任務管理;對接 SCADA 系統(tǒng),調(diào)用設備管理 (設備程序、設備數(shù)據(jù))模塊,可對設備進行集中線上管理,從操作規(guī)范、故障預測等方面延長設備使用壽命;通過報表看板顯示進度計劃、作業(yè)指導、設備狀態(tài)和生產(chǎn)統(tǒng)計分析等信息。
智能調(diào)度系統(tǒng)與生產(chǎn)線設備進行數(shù)據(jù)交互,可根據(jù)設備所傳遞的觸發(fā)指令、需求指令等信息,對 AGV 的中控系統(tǒng)發(fā)出調(diào)度指令。
主驅(qū)動裝配生產(chǎn)線調(diào)度流程(結(jié)合圖 2、圖 3) 如下:1)智能調(diào)度系統(tǒng)根據(jù)訂單信息,將裝配物料配送至卸貨區(qū)卸貨,隨后進行分揀裝框,并寫入物料信息; 2)將需清洗的小件清洗件人工上料小件清洗專機,經(jīng) 清洗后下線掃碼將物料信息傳遞至智能調(diào)度系統(tǒng),智能調(diào)度系統(tǒng)呼叫 AGV 將物料運送至已清洗小件緩存區(qū)(庫);3)小齒輪組件裝配專機根據(jù)計劃信息,呼叫 AGV 進行物料配送,將組裝完成的小齒輪組件運送至物料緩存區(qū);4)當總裝工位進行裝配時,通過終端發(fā)出物料需求給智能調(diào)度系統(tǒng),智能調(diào)度系統(tǒng)呼叫 AGV 將物料從緩存區(qū)運送至總裝工位。
通過信息化手段進行產(chǎn)品計劃管理及調(diào)度,實現(xiàn)裝配過程信息監(jiān)控及傳輸,增強產(chǎn)品裝配透明度,能更及時客觀地了解產(chǎn)品裝配進展和質(zhì)量信息,高效地進行質(zhì)量判定,大幅增強質(zhì)量追溯和分析能力。
三、裝配線工藝驗證
最終設計的盾構(gòu)機主驅(qū)動裝配生產(chǎn)線于 2023 年 7 月在鐵建重工廠房進行組裝調(diào)試,根據(jù)制定的布局及安裝方案,于同年 9 月順利完成安裝與調(diào)試,裝配生產(chǎn)線現(xiàn)場如圖 11 所示,通過盾構(gòu)機主驅(qū)動裝配生產(chǎn)線建設,有效地提高了裝配質(zhì)量及裝配效率,就單臺套盾構(gòu)機主驅(qū)動而言,節(jié)約組裝時間周期 20 %以上,同時也保障了生產(chǎn)安全。
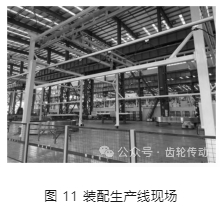
四、結(jié)語
本文針對盾構(gòu)機主驅(qū)動的裝配,完成了主驅(qū)動裝配生產(chǎn)線的整體布局,給出了主驅(qū)動零/ 部件自動化清洗、物料自動化轉(zhuǎn)運、小齒輪組件自動化裝配及緊固件扭矩管理等關(guān)鍵技術(shù)的實施方案,并通過搭載智能調(diào)度系統(tǒng)實現(xiàn)了裝配過程信息化管理。該裝配生產(chǎn)線自動化程度高,在減輕現(xiàn)場工人作業(yè)強度的同時,縮短裝配周期,提升工作效率及產(chǎn)品產(chǎn)出量。該裝配生產(chǎn)線投產(chǎn)后取得了良好的效果,對提高企業(yè)的經(jīng)濟效益具有重要意義,在業(yè)界具有示范性作用。
參考文獻.