齒輪是傳動系統中的關鍵零件,其失效形式有齒根彎曲疲勞、齒面接觸疲勞等,這些失效往往是由齒輪齒面或齒根的加工質量不高造成的。齒面的加工質量由齒面的表面粗糙度、硬度、滲層深度、齒參數等因素決定。為滿足齒面的加工質量,通常都是利用最終磨削加工來保證。在實際加工中,往往會采用高速磨削工藝方法。高速磨削工藝方法起源于德國,是一種以提高砂輪線速度為主要手段 來提升磨削效率和磨削質量的工藝方法,是磨削工藝的革命性躍變。通常將砂輪線速度45~150m/s 定義為高速磨削。
某型號齒輪齒數 42,模數 2.5,材料為鍛 9310,齒部及兩端軸頸滲碳層 0.6~0.9mm,表面硬度 HRC ≥ 60,齒形公差 0.006,齒向公差 0.007,兩端軸頸要求圓度 0.005,相互同軸度 Φ0.006,如圖1所示。該零件在滲碳淬火后精磨削工序中出現燒傷裂紋現象。磨削裂紋普遍存在于齒頂、齒端面近齒根處和兩端軸頸。
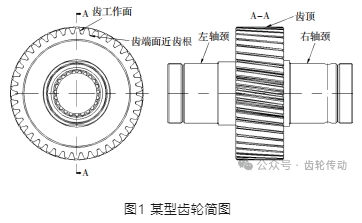
一、磨削燒傷理論
磨削燒傷是指磨削加工時,工件表面局部受高溫而產生的金相組織變化,特別是磨削表面在瞬時高溫的作用下,工件的表面局部受熱過高,發生不均勻退火,零件表層變軟,發黑或者發黃現象。磨削加工是通過砂輪磨粒的負前角擠壓切削高速運轉的零件表面過程,磨削金屬切削屑層少而薄,僅有不到10% 的切削熱量被帶走, 70%~80% 的熱量會由磨削表面傳入零件,故在零件磨削加工的表面區域溫度會急劇升高,尤其瞬時溫度可達到 800~1000℃,甚至更高。當溫度超過材料金相變化的臨界點時,就會在材料基體表面層發生組織變化,使零件表面層的硬度和強度極度下降。之后,零件表面開始冷卻直至最后冷卻,會引起零件表層的熱脹冷縮,造成自零件表面到內部各層產生各異的殘余應力。這些各異的 殘余應力就會引起顯微裂紋。
磨削燒傷產生后,基體表面的金相組織發生明顯的變化,就淬火鋼而言,其磨削燒傷特征如圖2所示。根據磨削瞬時產生溫度的高低,磨削燒傷的表層一般可分為回火燒傷(回火層)、淬火燒傷(過回火層和二次淬火層之間)和退火燒傷(二次淬火層和磨削表面之間)。
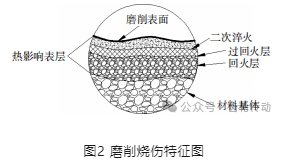
二、磨削燒傷變量因素
磨削加工面的熱影響層是由磨削熱量決定的。因而,一切能影響磨削熱量的變量都是改善磨削燒傷的變量因素,如砂輪、冷卻液、磨削參數等。
砂輪
砂輪是由磨料和結合劑以適當的比例混合,經壓制,干燥,燒結而成。它主要由磨粒、結合劑和空隙等3部分組成。磨粒相當于切削工具的切削刃,起切削的作用 ;結合劑使各磨粒位置固定,起支撐磨粒的作用 ;空隙則有助于排削和散熱的作用。磨削用的砂輪種類繁多,分類方法也有很多。通常有下列3種分類方法。
(1)按所用磨料,可分為普通磨料(剛玉和碳化硅等)砂輪、天然磨料和超硬磨料(金剛石和立方氮化硼等)砂輪。
(2)按形狀,可分為平形砂輪、斜邊砂輪、筒形砂輪、杯形砂輪、蝶形砂輪等。
(3)按結合劑,可分為陶瓷砂輪、樹脂砂輪、橡膠砂輪、金屬砂輪等。
冷卻液
冷卻液一般分為純油性冷卻液和水溶性冷卻液,純油性冷卻液具有潤滑性強、維護性低、防銹好、工件的光潔度高等優點 ;水溶性冷卻液具有冷卻性好、比較環保、成本低等優點,被高速先進機床廣泛采用。
磨削參數
磨削加工時,砂輪線速度、工件的速度、磨削進給量、砂輪修整頻率、冷卻液噴嘴角度等都是影響磨削加工的重要參數。
三、磨削加工試驗
為解決此件的磨削燒傷問題,同時探索變量因素對磨削燒傷的影響,開展磨削加工試驗。試驗試樣直接采用新的零件,設備采用高速萬能數控磨床(哈挺 HG-1000U), 砂輪選取立方氮化硼蝶形砂輪,冷卻液采用 QuakerCool 3750。磨削加工如圖3所示。試驗中以齒端面和軸頸為加工對象,分別從砂輪線速度、工件的速度、磨削進給量、砂輪的修整頻率、冷卻液噴射角度等方面進行加工調試。加工方式采用往復循環磨削模式。
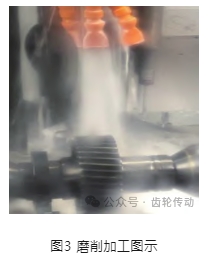
四、試驗結果及分析
砂輪線速度
砂輪線速度對磨削的影響,體現在磨削熱量。砂輪線速度越低,砂輪磨損越嚴重,生產率底,砂輪與工件單次接觸的時間就越長,單次產生的總接觸磨削熱量就越多,若磨削熱量沒有及時帶走,就易產生磨削燒傷。若砂輪線速度過高,磨粒切削刃鋒利程度下降,磨削不及時休整砂輪,就容易產生磨削燒傷。控制砂輪線速度,使單位時間產生的磨削熱量越低,帶走熱量越快,工件產生燒傷的概率就越低。工件速度 6m/min,磨削量 20μm,砂輪線速度與表面粗糙度的關系如圖4所示。
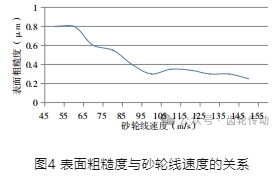
工件的速度
工件的旋轉速度對表面粗糙度的影響剛好與砂輪線速度的影響相反,增大工件速度時,單位時間內通過被磨表面的磨粒數減少,表面粗糙度值將增加,同時單位時間內磨削區域將增大,接觸的磨削熱量就越多,易出現磨削燒傷。砂輪線速度100m/s,磨削量20μm,工件速度與表面粗糙度的關系如圖5所示。
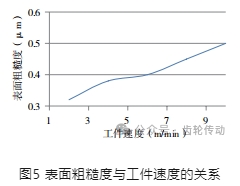
磨削進給量
磨削進給量越大,單位時間磨削接觸面積越多,被磨表面的粗糙度越大,產生的磨削熱量越多,易出現磨削燒傷。砂輪的縱向進給減小,工件表面的每個部件被砂輪重復磨削的次數增加,被磨表面的粗糙度值將減小,零件的表面粗糙度增加。砂輪線速度100m/s,工件速度6m/min,磨削進給量與表面粗糙度的關系如圖6所示。

砂輪的修整
磨削時間過長,工件材料過硬,砂輪失去自銳性,砂輪表面出現磨粒鈍化、砂輪表面空隙堵塞、外形失真等現象時,必須及時修整。修整的次數越多,砂輪單次加工時間就越短,砂輪表面出現磨粒鈍化速度就越低,零件表面的粗糙度就越高,工件出現燒傷的概率越低。砂輪線速度100m/s,工件速度6m/min,磨削量20μm,砂輪2次修正時間間隔與表面粗糙度的關系如圖7所示。
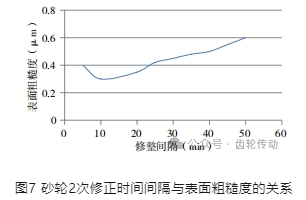
冷卻液噴嘴角度
磨削加工中,冷卻液是必不可少的環節,充足、高效率的冷卻液直接作用磨削接觸面,能夠有效地帶走磨削接觸熱,可有效地防止磨削燒傷。一般磨削都采用多噴嘴模式,調節多處噴嘴角度,使冷卻液最大限度的直接作用于磨削接觸點進行冷卻,能及時帶走磨削產生的熱量,可有效防止磨削燒傷。
五、結論
文章以實際加工中發現的磨削燒傷零件為例,闡述磨削燒傷機理,提出從砂輪線速度、工件的速度、磨削進給量、砂輪修整頻率、冷卻液噴嘴角度等變量方面控制磨削燒傷。通過大量試驗表明 :選用高速萬能數控磨床,立方氮化硼蝶形砂輪,砂輪線速度設為100m/s,工件速度設為6m/ min,采用單個循環(單個循環分成粗、半精和精3個階段,每個階段砂輪的進給速度分別為20μm/min、10μm/min、5μm/min)往復磨削加工,加上合理的冷卻液噴射角度,解決了此次零件的硬化面磨削燒傷問題。總結了零件表面加工質量和上述變量之間的關系,為后續類似零件的磨削加工及燒傷防控提供了加工依據。
參考文獻略.