弧齒錐齒輪是現(xiàn)代機(jī)械傳動(dòng)領(lǐng)域中的關(guān)鍵零件,在弧齒錐齒輪制造過程中,因機(jī)床誤差、熱變形等不可控因素,使輪齒的實(shí)際齒面偏離理論齒面,也使得基于理論齒面進(jìn)行的 TCA(齒面接觸分析)、LTCA(加載齒面接觸分析)的分析結(jié)果失去意義。為了調(diào)整齒面形狀,消除齒面偏差帶來的影響,傳統(tǒng)上使用比例修正的方法,這種方法對(duì)于操作人員的經(jīng)驗(yàn)要求較高。現(xiàn)在多使用齒輪測(cè)量中心來獲取齒面偏差,通過對(duì)加工參數(shù)的修正來實(shí)現(xiàn)對(duì)齒面幾何精度的控制。
針對(duì)齒面形狀控制的研究,李麗霞研究了機(jī)床調(diào)整誤差對(duì)弧齒錐齒輪齒面幾何精度的影響規(guī)律,建立了機(jī)床調(diào)整誤差補(bǔ)償?shù)臄?shù)學(xué)模型;曹康對(duì)螺旋錐齒輪機(jī)床調(diào)整參數(shù)的誤差敏感性和齒面誤差反調(diào)修正進(jìn)行了研究;王志永針對(duì)機(jī)床誤差對(duì)螺旋錐齒輪齒形的影響規(guī)律進(jìn)行了研究,并通過實(shí)驗(yàn)驗(yàn)證了分析結(jié)果的正確性;田程等通過結(jié)合機(jī)床調(diào)整參數(shù)的敏感度系數(shù)向量與實(shí)際測(cè)量齒面誤差向量的相關(guān)性,對(duì)齒面誤差進(jìn)行了優(yōu)化。聶少武等通過用二階曲面近似表達(dá)齒面拓?fù)淦睿瑢X面拓?fù)湫扌畏纸獬?5 個(gè)方向,并建立了對(duì)應(yīng)的修正數(shù)學(xué)模型,反求出了修形齒面的小輪加工參數(shù);李天興等分析了齒輪齒面齒形誤差及其影響因素,建立了機(jī)床參數(shù)與齒面齒形誤差的對(duì)應(yīng)關(guān)系。李其明等在機(jī)床調(diào)整參數(shù)靈敏度分析的基礎(chǔ)上,對(duì)齒形誤差修正方法進(jìn)行了研究,分析了機(jī)床調(diào)整參數(shù)對(duì)齒形誤差的影響。張宇研究了螺旋運(yùn)動(dòng)及刀具參數(shù)對(duì)雙重螺旋法加工齒面特征的影響規(guī)律;宋碧蕓等人基于齒面幾何誤差控制模型對(duì)加工參數(shù)進(jìn)行了敏感性分析,利用改進(jìn)的 L-M 方法求出了加工參數(shù)補(bǔ)償量。張彤研究了變性法和刀傾法小輪的各項(xiàng)機(jī)床加工參數(shù)誤差對(duì)齒形誤差的影響規(guī)律。
目前國內(nèi)企業(yè)研制的數(shù)控弧齒錐齒輪加工機(jī)床都具備高階運(yùn)動(dòng)功能,包括滾比修正、螺旋運(yùn)動(dòng)修正、垂直運(yùn)動(dòng)修正等。但因缺少成套的計(jì)算軟件,在實(shí)際切齒計(jì)算時(shí)最多用到三階滾比修正系數(shù),不能發(fā)揮出數(shù)控機(jī)床的萬能運(yùn)動(dòng)特性。同時(shí),在對(duì)輪齒齒面形狀進(jìn)行調(diào)整時(shí),雖然利用齒輪測(cè)量中心測(cè)量出了輪齒的齒面偏差,但是并不清楚高階滾比修正系數(shù)對(duì)齒面拓?fù)湫螤畹挠绊懸?guī)律。現(xiàn)有文獻(xiàn)中均未對(duì)高階滾比修正系數(shù)對(duì)弧齒錐齒輪齒面形狀的影響進(jìn)行深入研究。
論文針對(duì)上述情況,構(gòu)建包含高階滾比修正系數(shù)的齒面數(shù)學(xué)模型,探究高階滾比修正系數(shù)對(duì)弧齒錐齒輪齒面形狀的影響規(guī)律,為弧齒錐齒輪實(shí)際加工過程中的齒面調(diào)整提供理論依據(jù)。
一、齒面數(shù)學(xué)建模
基于齒輪嚙合原理和矢量運(yùn)算方法,根據(jù)刀具和齒坯的相對(duì)運(yùn)動(dòng)和相對(duì)位置關(guān)系,建立齒面數(shù)學(xué)模型。以左旋齒輪為例,左旋齒輪在機(jī)床調(diào)整位置時(shí)的情況如圖 1 所示。
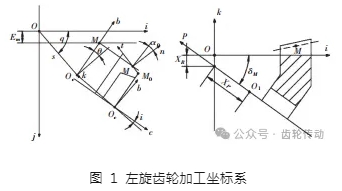
在坐標(biāo)系 σ = {O;i;j;k}中,O 是機(jī)床的中心,i、 j、k 分別為坐標(biāo)軸正方向的單位矢量。i - j 平面是機(jī)床平面,k 的正方向指向搖臺(tái)體內(nèi)。Oc 為刀尖平面與刀盤軸線的交點(diǎn),O1 為設(shè)計(jì)時(shí)的交叉點(diǎn)。b 為刀盤軸線在機(jī)床平面內(nèi)的投影。c 為刀盤軸線的單位矢量。Em 為垂直輪位,S 為徑向刀位,q 為角向刀位,矢量 p 為工件的軸線,XB 為床位,Xp 為水平輪位修正量,δM 為輪坯安裝角。這些參數(shù)可以通過弧齒錐齒輪加工計(jì)算軟件計(jì)算得到,或者由機(jī)床的實(shí)際加工調(diào)整參數(shù)得到。
刀具切削刃由兩部分組成,其中直線段切削刃生成輪齒的工作齒面,圓弧部分生成輪齒的齒根過渡圓角部分,因測(cè)量齒形偏差時(shí)設(shè)置了收縮量,齒根過渡圓角部分一般都不在檢測(cè)范圍內(nèi),以下只考慮直線段切削刃及其生成的工作齒面。
切削刃上任一點(diǎn) M 的坐標(biāo),即切削刃的矢量方程 rc 為:

式中,r0 為刀尖頂點(diǎn)的矢量方程,s1 為切削刃上任一點(diǎn)M到刀尖頂點(diǎn)M0的距離,t1 為母線M0M方向上的單位矢量。
被加工齒面與刀盤的切削面是共軛曲面,根據(jù)產(chǎn)形輪與齒輪之間的相對(duì)運(yùn)動(dòng)關(guān)系,引入高階滾比修正系數(shù),此時(shí):

工件的角速度為:
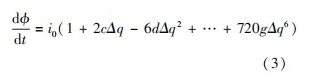
上式中,i0 為滾比,Δq 為搖臺(tái)角改變量,2c、6d、24e、120f、720g 分別為二階至六階的滾比修正系數(shù)。
由齒面嚙合方程可求得齒面上的點(diǎn)和 M 點(diǎn)共軛接觸時(shí)的 q、θ 以及工件轉(zhuǎn)角 ?。進(jìn)而可求得工件齒面上的點(diǎn)以 O1為原點(diǎn)的徑矢 rw 及其法矢 nw:
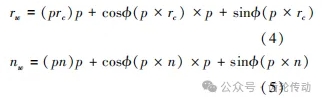
二、齒面離散點(diǎn)參數(shù)的計(jì)算
計(jì)算理論齒面離散點(diǎn)空間坐標(biāo)及其法矢是進(jìn)行齒面誤差測(cè)量和齒面形狀分析的前提條件,同時(shí)也是實(shí)現(xiàn)弧齒錐齒輪數(shù)字化制造的關(guān)鍵環(huán)節(jié)之一。為了實(shí)現(xiàn)齒面的精密測(cè)量以及計(jì)算理論齒面與實(shí)際齒面之間的誤差,需要對(duì)齒面進(jìn)行離散化處理,即在弧齒錐齒輪理論齒面的旋轉(zhuǎn)投影面上規(guī)劃一定的測(cè)量網(wǎng)格。
為了反映齒面的形狀特征,一般在齒高方向取 5 行,在齒長方向取 9 列,共 計(jì) 45 個(gè)離散點(diǎn),如圖 2 所示。根據(jù)美國齒輪標(biāo)準(zhǔn),在齒寬方向,大端和小端各收縮齒面寬的 10%,在齒廓方向,齒頂和齒根各收縮全齒高的 5% 且不能小于 0.6 mm。收縮后的齒面各邊界應(yīng)與收縮前的齒面各邊界平行,并根據(jù)網(wǎng)格點(diǎn)的數(shù)量將齒面各邊界等距均分。在圖 2 所示的坐標(biāo)系下,可以計(jì)算出各離散點(diǎn)在以交叉點(diǎn) O1 為原點(diǎn)的坐標(biāo)系中的坐標(biāo)值(x(i,j),y(i,j)),其中 i = 1~9,j = 1~5。
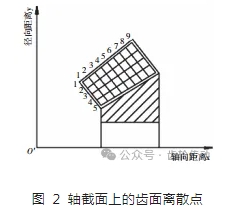
如圖 2 所示,設(shè)齒面上的 M 點(diǎn)沿齒輪軸線 p 到 O1 的距離為 x,到齒輪軸線 p 的距離為 y,則有:

式中的 x、y 是 q 和 θ 的函數(shù),給定了 q 和 θ 的值,再根據(jù)式(4)和式(5)就能求得 x、y 的值。如果給定了齒面上離散點(diǎn)的坐標(biāo)值,就可以利用二元迭代的方法求解其對(duì)應(yīng)的 q 和 θ,隨后再利用式(2)、式 (3) 進(jìn)而求得理論齒面上對(duì)應(yīng)每一個(gè)離散點(diǎn)的徑矢 rw 和法矢 nw,此后再經(jīng)過一次坐標(biāo)變化,即可將其轉(zhuǎn)換到測(cè)量坐標(biāo)系中。利用三坐標(biāo)測(cè)量機(jī)或者齒輪測(cè)量中心就可以根據(jù)齒面離散點(diǎn)的空間坐標(biāo)和法矢進(jìn)行實(shí)際齒面齒形誤差的測(cè)量。
三、齒形改變量的計(jì)算
根據(jù)齒輪切齒加工的刀具參數(shù)和機(jī)床調(diào)整參數(shù),運(yùn)用上文所建立的齒面數(shù)學(xué)模型,可以得到理論齒面上各個(gè)離散點(diǎn)所對(duì)應(yīng)的徑矢 rw 和法矢 nw 。此外,設(shè)定一組包含誤差的刀具參數(shù)和機(jī)床調(diào)整參數(shù),即可求得誤差齒面上的各個(gè)離散點(diǎn)對(duì)應(yīng)的徑矢 rw ′ 和法矢 nw ′。將理論加工參數(shù)對(duì)應(yīng)的齒面定義為理論齒面,將改變后的加工參數(shù)對(duì)應(yīng)的齒面定義為實(shí)際齒面,如圖 3 所示。
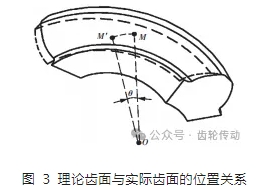
改變機(jī)床調(diào)整參數(shù)后,實(shí)際齒面會(huì)偏離原始齒面,為了對(duì)比實(shí)際齒面相對(duì)于理論齒面的變化和分析齒面誤差,需將實(shí)際齒面旋轉(zhuǎn),使齒面網(wǎng)格中點(diǎn) M′ 與理論齒面中點(diǎn) M 重合,設(shè)旋轉(zhuǎn)的角度為 θ。旋轉(zhuǎn)后理論齒面上任意一點(diǎn)到實(shí)際齒面上對(duì)應(yīng)該點(diǎn)之間法線方向的偏差就是該點(diǎn)的誤差值。齒輪測(cè)量中心在測(cè)量弧齒錐齒輪時(shí),以齒面的中點(diǎn)為參考點(diǎn),以“S”形逐點(diǎn)移動(dòng)進(jìn)行測(cè)量。再通過軟件的處理,就得到了齒面上各個(gè)網(wǎng)格點(diǎn)對(duì)應(yīng)的齒面誤差,以此就能繪制出齒面誤差拓?fù)鋱D。
以工廠實(shí)際生產(chǎn)的某弧齒錐齒輪小輪為例(采用雙重螺旋法加工),分析各階滾比修正系數(shù)對(duì)齒面形狀的影響規(guī)律。齒輪副的參數(shù)如表 1 所示,加工輪齒的機(jī)床調(diào)整參數(shù)和刀具參數(shù)如表 2 所示。收縮量設(shè)置為:小端收縮量 1.5 mm,大端收縮量 2.5 mm,齒頂收縮量 1 mm,齒根收縮量 1.7 mm。
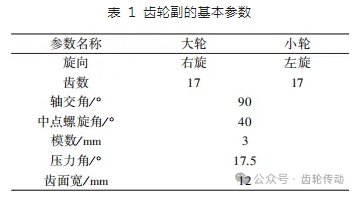
為了分析各高階滾比修正系數(shù)對(duì)齒面形狀的影響規(guī)律,假定二階至六階滾比修正系數(shù)的改變量依次為:+0.02、+0.2、+2、+20、+200。利用 VB 編制齒形分析軟件,對(duì)每個(gè)改變量進(jìn)行齒形誤差計(jì)算并繪制齒面誤差改變拓?fù)鋱D。
計(jì)算分析結(jié)果如圖 4 所示,圖中粗實(shí)線表示理論齒面,細(xì)實(shí)線表示理論齒面低于實(shí)際齒面,細(xì)虛線表示理論齒面高于實(shí)際齒面,在齒輪凹凸兩面的 4 個(gè)角點(diǎn)標(biāo)有實(shí)際齒面在該點(diǎn)處相對(duì)于理論齒面的齒形誤差值,誤差值單位為 μm。
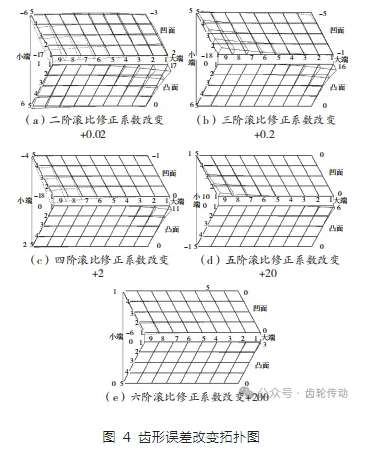
四、滾比修正系數(shù)對(duì)齒面形狀的影響規(guī)律
在實(shí)際加工弧齒錐齒輪時(shí),工作人員通過齒輪測(cè)量中心測(cè)量齒面誤差或者進(jìn)行滾檢觀察齒面接觸區(qū),再通過改變機(jī)床調(diào)整參數(shù)對(duì)輪齒的齒面幾何形狀,齒輪副接觸區(qū)的大小、位置和方向進(jìn)行調(diào)整。不同的機(jī)床調(diào)整參數(shù)對(duì)齒面形狀的影響程度不同,根據(jù)齒面的形狀,將誤差齒面表示為二階曲面的形式,將齒面誤差對(duì)各階滾比修正系數(shù)的變化趨勢(shì)分解為 5 個(gè)誤差敏感系數(shù)。圖 5 為齒面誤差二階曲面,圖中原點(diǎn)與齒面網(wǎng)格中點(diǎn)重合,齒長方向?yàn)閄,齒高方向?yàn)?Y,Z 為齒面形狀誤差,用二階曲面近似的表達(dá)齒面形狀誤差拓?fù)鋱D,其表達(dá)式為:

式中,a1 為螺旋角誤差敏感系數(shù),a2 為壓力角誤差敏感系數(shù),a3 為齒面撓率誤差敏感系數(shù),a4 為齒長曲率誤差敏感系數(shù);a5 為齒高曲率誤差敏感系數(shù)。一階系數(shù) a1 、a2 是對(duì)齒面傾斜角度的表達(dá),二階系數(shù) a3 、a4 、a5 是對(duì)誤差齒面彎曲程度的表達(dá)。

將齒面網(wǎng)格上任意一點(diǎn)的齒面誤差用矩陣表示為:
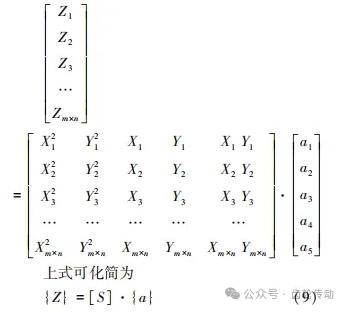
式中,Z 為各個(gè)離散點(diǎn)的齒形誤差,矩陣 S 為誤差矩陣,其數(shù)值由離散點(diǎn)的坐標(biāo)確定,詳細(xì)推導(dǎo)過程參考文獻(xiàn)。每改變一項(xiàng)機(jī)床調(diào)整參數(shù),與之對(duì)應(yīng)的齒面形狀誤差 Z 也會(huì)隨之發(fā)生改變,根據(jù)計(jì)算出的離散點(diǎn)坐標(biāo),可求得每個(gè)機(jī)床調(diào)整參數(shù)對(duì)應(yīng)的誤差敏感系數(shù)。式(9)為超靜定方程組,利用最小二乘法可求得其最小二乘解,即:

以上述齒輪副為例,計(jì)算小輪在各高階滾比修正系數(shù)改變下齒面形狀誤差對(duì)應(yīng)的誤差敏感系數(shù)。計(jì)算結(jié)果如表 3、表 4 所示。
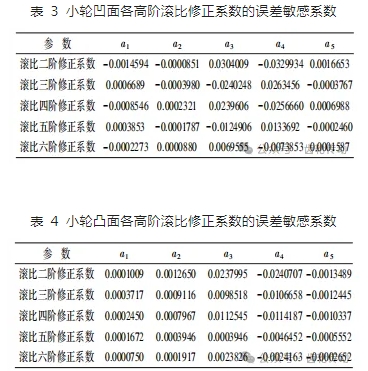
誤差敏感系數(shù)越大,則與之對(duì)應(yīng)的高階滾比修正系數(shù)改變量對(duì)齒面形狀的影響越大,結(jié)合圖 3 對(duì)表 3、表 4 的計(jì)算結(jié)果進(jìn)行分析可知:
1)高階滾比修正系數(shù)對(duì)齒形的影響主要作用在凹面小端的齒頂和凸面大端的齒頂,對(duì)齒面中部和齒根的影響較小。
2)輪齒凹面,在齒面傾斜角度方面,各階滾比修正系數(shù)對(duì)壓力角與螺旋角的影響程度大致相同;在齒面彎曲程度方面,一階滾比修正對(duì)齒面撓率的影響較大,對(duì)齒高方向曲率影響最小;二階滾比修正系數(shù)對(duì)齒長方向曲率影響最大,對(duì)齒面撓率影響最小;三階到六階滾比修正系數(shù)均對(duì)齒長方向曲率影響最大,對(duì)齒高方向曲率影響最小。
3)在輪齒凸面,在齒面傾斜角度方面,二階到四階滾比修正系數(shù)對(duì)壓力角的影響均略大于對(duì)螺旋角的影響,五階、六階滾比修正系數(shù)對(duì)壓力角的影響遠(yuǎn)大于對(duì)螺旋角的影響;在齒面彎曲程度方面,二階到六階滾比修正系數(shù)均對(duì)齒面撓率的影響最大,對(duì)齒長方向的曲率影響最小。
4)齒輪大端的凹凸兩面變化趨勢(shì)大致相同,而小端則是二階、四階、六階變化趨勢(shì)相同,凹面實(shí)際齒面低于理論齒面,凸面實(shí)際齒面高于理論齒面;三階、五階變化趨勢(shì)相同,凹面實(shí)際齒面高于理論齒面,凸面實(shí)際齒面低于理論齒面。
為了驗(yàn)證論文的正確性,在H350GH 數(shù)控螺旋錐齒輪磨齒機(jī)上,根據(jù)各階滾比修正系數(shù)的改變量進(jìn)行了磨削試驗(yàn),如圖 6 所示。并利用齒輪測(cè)量中心對(duì)齒形誤差進(jìn)行了檢測(cè),如圖 7 所示。檢測(cè)得到的齒面誤差拓?fù)鋱D的齒面形狀變化趨勢(shì)、各點(diǎn)對(duì)應(yīng)的齒面誤差值和本文分析得到的結(jié)果基本一致,細(xì)微的差別是由于隨機(jī)誤差與測(cè)量誤差造成的。因篇幅所限,論文僅列出滾比修正二階系數(shù)改變+ 0.02 時(shí)的檢測(cè)結(jié)果,如圖 8 所示。
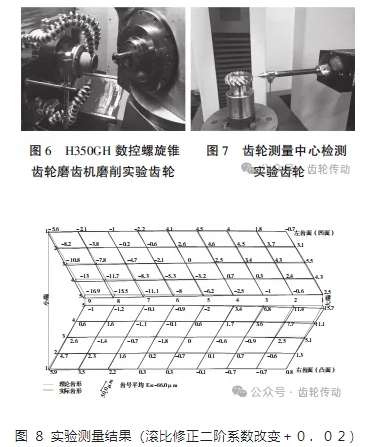
五、結(jié)束語
建立了引入高階滾比修正系數(shù)的弧齒錐齒輪齒面數(shù)學(xué)模型,開發(fā)了齒形誤差分析軟件,借助二階曲面對(duì)齒面誤差的近似表達(dá),分析了高階滾比修正系數(shù)的改變對(duì)輪齒齒形的影響規(guī)律,為弧齒錐齒輪實(shí)際加工過程中機(jī)床功能的合理運(yùn)用、齒形調(diào)整、齒面接觸區(qū)的調(diào)整和齒形誤差的修正提供了理論依據(jù)。