航空發動機輸出動力,航空動力傳動系統通過機械分扭裝置,將動力傳遞至相關部件。作為航空動力傳動系統的基礎零部件,航空齒輪在特定動態、高溫、高速、重載等復雜工況條件下服役,為保障動力傳輸發揮著重要的作用,航空齒輪零部件的可靠性程度直接關乎航空飛行器的服役效能與安全性。
出于減重需要,航空齒輪通常采取“結構-功能一體化”設計,零件結構異常復雜、高度集成,沉余尺寸相對較低。齒輪在工作時,齒根部位受到彎曲應力作用,易產生疲勞斷裂,而齒面部位則受到接觸應力作用,易于產生齒面表面的剝落。相對于汽車、機械行業等常規齒輪,航空齒輪服役工況苛刻,同時承受劇烈的交變載荷和沖擊載荷,因此,航空齒輪在選材時,通常選取中低碳合金鋼材料,通過滲碳、氮化、氰化等化學熱處理表面改性方式強化齒面。在確保心部組織具有良好淬透性及抗沖擊韌性的同時,齒形面因表面強化兼具優異的耐磨性。
長期以來,我國航空齒輪材料始終處于被動仿制階段,隨著航空飛行器家族譜系的不斷細分與完善,相應也帶動了我國航空齒輪材料的迭代發展,但在航空齒輪結構鋼的設計強化理論及合金化機理方面,始終停滯不前,亟待加強相關基礎自主研究工作,補齊相關技術、理論短板。本工作對航空動力傳動系統滲碳齒輪材料的代際發展、組分特征與強化機制進行綜述,以期促進航空齒輪結構鋼的良性發展。
一、第一代滲碳齒輪鋼
自 20 世紀 60 年代,美國將制造高純凈度軸承鋼 VIM-VAR 雙真空熔煉技術,導入高性能齒輪鋼冶煉后,大大提升了齒輪鋼性能,也促使軸承鋼與齒輪鋼向著逐漸融合、形成同源發展,幾乎所有的中低碳軸承鋼均可用于齒輪加工制造,因此,西方學者根據軸承鋼、齒輪鋼的服役溫度,將現有中低碳軸承鋼與齒輪鋼歸集并劃分為三個代際。
我國航空用第一代滲碳齒輪鋼材料,初期以仿制蘇聯為主,典型鋼種為 12CrNi3A、12Cr2Ni4A、14CrMnSiNi2MoA、18Cr2Ni4WA、20CrNi3A、20Cr- 2Ni4A 等,20 世紀 80 年代開始,隨著我國航空工業對外合作力度的加大,相繼引入18CrNi4A(意大利18NC16)、9310(美國)及16Cr3NiWMoVNbE(俄羅斯)、17CrNiMo6(德國)。航空第一代滲碳齒輪鋼合金化成分見表 1 ,服役溫度通常不超過 200 ℃。
表 1 常用航空第一代滲碳齒輪鋼牌號及合金成分(質量分數/%)
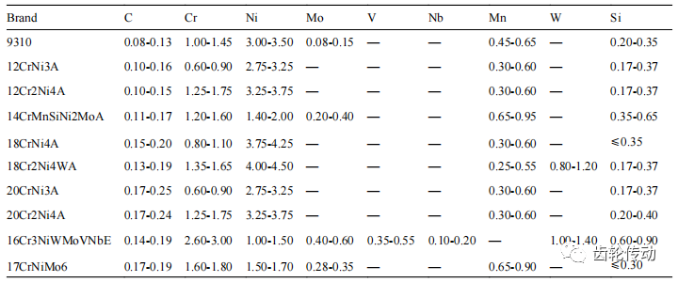
通過表1可以看出,航空用第一代滲碳齒輪鋼基本上可以分為 Cr-Ni、Cr-Ni-W 及 Cr-Ni-Mo 三大合金體系。Cr-Ni 系合金含量及合金化元素種類相對較少,經濟性方面 Cr-Ni 材料性價比最高,屬于典型的低碳低合金鋼。因材料體系中缺乏必要的強碳/氮化物形成元素,基體比強度及淬透性相對較低,滲碳化學表面改性之后,滲層組織淬硬層的硬度及回火抗力最低,承載能力及耐溫服役裕度最低。
為提高 Cr-Ni 合金體系強度及滲層組織回火抗力,適度提升基體淬透性,冶金學家向 Cr-Ni 系中適當引入少量強碳/氮化物形成元素,形成 Cr-Ni-Mo 與 Cr-Ni-W 合金體系,屬于低碳中合金鋼范疇。其中,作為航空第一代滲碳齒輪鋼 Cr-Ni-W 系中的典型代表,18Cr2Ni4WA 鋼由于高熔點 W 元素的引入,基體淬透性、熱強性及耐磨性均得到顯著提升,是目前已知第一代滲碳齒輪鋼中,唯一既可在調質狀態下使用,又可進行滲碳、氮化表面改性強化的鋼種,具有極好的熱處理工藝加工性能。
9310 鋼源自美國,初期應用于汽車齒輪行業,因其成本低、強度高、韌性好、具有一定淬透性及可焊性,逐步推廣應用于制造中重載荷、中大截面尺寸航空動力傳動系統中的齒輪、齒輪軸、旋翼軸等構件,對應的國內材料牌號 12CrNi3MoA,9310 在 Cr-Ni-Mo 系低碳低合金鋼體系中,鎳含量最高,具有最高的淬透性。
17CrNiMo6 材料是國外重載齒輪使用相對較為成熟的牌號,我國國產化后,在航空、汽車、減速器、重型機械等領域均得到了顯著的應用,通過“引 Mo 降 Ni”,合理降低了材料制造成本,是研發較為成功 Cr-Ni-Mo 系鋼種,適用于模數≥12 的重載齒輪制造。
16Cr3NiWMoVNbE 材料雖然劃歸于在航空第一代滲碳齒輪鋼,優異的合金化設計,使其具備 300 ℃ 中高溫區服役的能力,借助特殊表面改性工藝路徑及方法,可提升為第二代滲碳齒輪鋼。提升 16Cr3NiWMoVNbE 材料服役溫度,有多種工藝路徑及方法,除常規可控氣氛飽和滲碳、煤油滴注超飽和滲碳外,還可通過脈沖正逆序滲碳、高溫滲碳復合低溫氮化、可控氣氛變溫變碳勢非飽和滲碳等非常規工藝路徑加以實現。
二、第二代滲碳齒輪鋼
隨著航空技術的發展,航空動力傳輸的扭矩急劇提升,航空軸承、齒輪等零部件的服役溫度大幅提升至 200 ℃ 以上,原有的第一代滲碳齒輪鋼,因基體合金化程度相對較低,合金化元素含量相對較少,滲碳表面改性后,滲層組織的回火抗力不足。在高荷載作用下,齒輪工作齒面溫度顯著增加,滲層組織硬度大幅下降。
與軸承相比,齒輪的受力狀態更加復雜,除在接觸面法向方向產生接觸應力外,周向方向輪齒產生彎曲應力,部分斜齒及錐齒輪還產生軸向應力。通常情況下,接觸疲勞強度與齒輪接觸面硬度值二次方呈正比,在循環接觸應力作用下,齒面硬度的下降,直接導致齒輪接觸表面麻點、滲層剝落。對于轉速相對較高、荷載相對較大的中重型齒輪,輪齒齒面嚙合滑動速度較高,在滑動接觸區域產生高溫,滲碳齒輪回火抗力不足時,齒面極易產生膠合現象,對航空動力傳動系統整體造成重大影響。
針對上述問題,冶金學家利用含 Mo 合金鋼“二次硬化”原理,設計、研制出低碳中高合金 Cr-Ni-Mo 系的第二代滲碳齒輪鋼。第二代滲碳齒輪常見牌號有 EX 53、Pyrowear 53、Py rowear 675、M 50Ni L、CBS 600、CBS 1000M、Vasco x-2 等,常見牌號合金化成分如表 2 所示,第二代滲碳齒輪鋼的服役溫度上限提升至 350 ℃。
表 2 常用航空第二代滲碳齒輪鋼牌號及合金成分(質量分數/%)
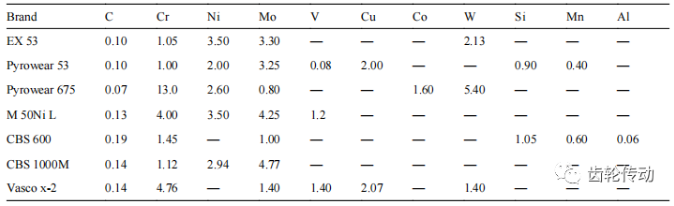
與第一代滲碳齒輪鋼相比,第二代滲碳齒輪鋼合金化元素的含量及種類均有提升,其中 Mo 元素的含量提升最為顯著。表 1 中 16Cr3NiWMoVNbE 中的 Mo 質量分數最高,達到 0.60%,而第二代滲碳齒輪鋼中,除 Pyrowear 675 和 CBS 600(對應美國航空航天材料標準牌號為 AMS 5930 和 AMS 6255)之外,Mo 元素質量分數普遍超過 1.0%。
第二代滲碳齒輪鋼中,Cu、Al 元素主要發揮彌散析出強化作用,Co 元素可增加基體的熱強性,W 與 Mo 元素協同,能夠形成較強的二次硬化效果;Mo、Cu 元素協同,能夠顯著增加材料的淬透性,用于制造重型齒輪零件。第二代滲碳齒輪鋼整體碳含量普遍偏低,低碳含量有助于基體沖擊韌性的改善。第二代滲碳齒輪鋼中,國內常用的牌號為 Pyrowear 53,國產化后對應的牌號為 10CrNi2Mo3- Cu2V,由美國 Carpenter Technology 公司研制,對應美國航空航天材料標準牌號為 AMS 6308。鋼中含有 2.00% 左右的 Cu,Cu 在基體中除發揮一定的耐蝕作用之外,更主要的目的是利用其在基體中彌散析出強化。
該材料淬火后,在 205~350 ℃ 回火,隨著回火溫度的提高,抗拉強度、塑性、沖擊韌性及硬度均變化不大,因此,Pyrowear 53 材料滲碳、淬火、冰冷回火后的回火溫度通常不超過 350 ℃。當回火溫度≥350 ℃ 時,尤其在 400~450 ℃ 回火,雖然強度顯著提高,但沖擊韌性快速下降,450 ℃ 左右時,強度及沖擊韌性分別達到極大值與極小值,此時富 Cu 相的析出達到峰時效狀態,并誘發二次強化脆化現象,繼續提高回火溫度,富 Cu 相進入過時效狀態,基體強度下降。
在第二代滲碳齒輪鋼中,Pyrowear 53 鋼的整體合金化程度相對較低,該材料提升接觸疲勞壽命效果顯著低于以 M50NiL 為代表的其他材料牌號,其 10% 接觸疲勞壽命是 9310 鋼的 2 倍,同時,該材料兼具高性價比,因此,在美、歐及我國航空齒輪行業均得到相對廣泛的應用,常用于滲碳表面改性,雖然 Pyrowear 53 鋼在 400~600 ℃ 范圍內硬度在 HRC39~42,基體塑性及沖擊韌性均大幅下降,不適于氮化表面改性,可進行氰化改性。M50NiL 是瑞典 SKF 公司 20 世紀 80 年代專門為美國空軍研制的一種新型滲碳軸承鋼,對應美國航空航天材料標準牌號為 AMS 6278。M50 高溫軸承鋼通過“降 C 增 Mo”,將基體萊氏體組織轉變為板條馬氏體組織,斷裂韌度提高 2 倍以上。同時,基體殘余奧氏體的消除,使其尺寸穩定性得到大幅提升。M50NiL 經過滲碳、淬火、冰冷處理、回火后,可以在 316 ℃ 長期服役,是第二代滲碳齒輪鋼中的典型代表,可進行滲碳、氰化及高溫滲碳+低溫氮化復合強化三種化學熱處理表面改性。雙真空熔煉的 M50NiL 的疲勞壽命,雖然是 9310 的 13.2 倍,由于材料的合金元素含量達到 12% 以上,材料制造成本過高,滲碳時需采用低壓真空滲碳工藝,除做特殊要求外,極少用于齒輪加工制造,主要用于加工制造高性能耐溫軸承。
三、第三代滲碳齒輪鋼
美國 Latrobe Specialty Steel Company 于 20 世紀 90 年代在 BG42(14-4 Mo)不銹軸承鋼和 AFC77 超高強度沉淀硬化不銹鋼基礎之上,成功研制出可滲碳的耐溫軸承鋼 CSS-42L,材料滲碳后滲層組織具有優異的高溫紅硬性、耐磨性及耐蝕性,心部組織保持著極高的強度與斷裂韌度,服役耐溫性較第二代滲碳齒輪鋼 M50NiL 提升 100 ℃ 以上。CSS-42L 成為首個在實踐中得到應用的第三代滲碳齒輪鋼牌號,開創了第三代滲碳齒輪鋼的研制先河。目前已知的第三代滲碳齒輪鋼常見牌號,均由美國研制,合金化成分見表 3,行業普遍認為第三代滲碳齒輪鋼的服役溫度≤500 ℃。從 表 3 可以看到,第三代滲碳齒輪鋼的 5 種牌號,除 Ferrium CS62 外,合金化含量均超過 30%,屬于典型的低碳超高合金鋼范疇。與傳統的第二代滲碳齒輪鋼相比,第三代滲碳齒輪鋼通過大幅提高 [Cr+Ni] 合金化元素總和,使基體耐蝕性得到大幅提升,基體固溶淬火、(深)冷處理后,由常規馬氏體結構鋼轉變為耐蝕性更好的馬氏體不銹鋼,引入并大幅增加 Co 合金化元素,使得第三代滲碳齒輪鋼具備 400 ℃ 以上的優異高溫熱穩定性,確保齒輪在無油干運轉狀態仍表現出良好的高溫紅硬性。
表 3 航空第三代滲碳齒輪鋼牌號及合金成分(質量分數/%)
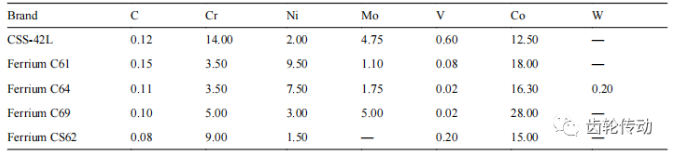
表 3 中的 CSS-42L 與 Ferrium 系列四種鋼的合金化設計有著本質性差異,CSS-42L 主合金中 Cr 含量超過 10%,而 Ferrium 系列除 Ferrium CS62 外,均不大于 5%,CSS-42L 中的 Ni、Co 含量顯著低于 Ferrium 系列。
第三代滲碳齒輪鋼屬于高熵值超高合金特殊鋼,我國在這一領域整體起步較晚,整體研發能力與制造水平普遍偏低,在均質化凝固、潔凈度、雜物控制及相關熱加工工藝技術成熟度等方面,與美、歐、日本等先進國家存在較大差距,目前完全處于仿制階段,尚未形成自主材料研發能力。
美國成功研制出 CSS-42L 第三代滲碳齒輪鋼后,我國北京鋼鐵研究總院開始仿制,進行了材料工程化應用研究探索工作。隨后,中國航發航材院、寶鋼、哈爾濱工業大學、昆明理工大學等相繼開展了國產化材料牌號研制及相關熱處理工藝制度的研究工作,目前已知 CSS-42L 衍生國產化材料牌號除15Cr14Co12Mo4Ni2VNb、15Cr14Co12Mo5Ni 兩種之外,還有 14Cr14Co13Mo4、BG800。
CSS-42L 中含有大量 Cr、Mo、V 等碳化物形成元素,在高溫滲碳過程中,這些合金化元素能夠與活性碳原子發生強化的“化學拖拽”,遲滯活性碳原子向心部基體的擴散,并產生上坡擴散,在滲層組織中原位析出二次特殊碳化物 M7C3、M23C6。這些二次特殊碳化物的模量、硬度與熔點顯著高于傳統的第一代、第二代滲碳齒輪鋼(M50NiL 除外)析出的 Fe3C 型常規滲碳體,通過滲碳工藝調控,CSS- 42L 可在滲層組織中持續、大量析出二次特殊碳化物,使滲層組織具有十分優異的高溫紅硬性及減摩耐磨效果。CSS-42L 是目前已知滲碳鋼中,滲碳改性后硬度能夠達到最高的牌號,滲碳改性后的滲層表面硬度可高達 HRC67~72,與硬質合金刀具硬度數值接近,復合低溫氮化后,滲層表面硬度可進一步得到提升。CSS-42L 材料滲碳過程中,如果活性碳原子持續、大量擴散滲入,滲層組織原位形成 的二次特殊碳化物將沿特定的金屬學位相關系,以魏氏針狀組織形式大量析出。目前僅能通過脈沖低壓真空滲碳工藝方法,有效調控單一子脈沖滲碳循環載入的活性碳原子總量,合理設定子脈沖程序中的強滲時間與擴散時間的數值比值,杜絕魏氏組織的析出。
CSS-42L 國產化材料雖然初步解決了滲層組 織碳化物析出形態控制問題,但基于我國脈沖低壓真空滲碳工藝基礎原理研究尚處于起步階段的現實,相關材料滲層組織碳化物形態優化、滲層組織超高硬度滲碳工藝實現、現有工藝可控性誘發的批量化生產等現實工程問題,始終有待提升,也嚴重制約著相關材料的工程化應用。CSS-42L 可進行高溫滲碳、固溶淬火、低溫氮化復合強化,強化效果較為顯著。結合必要的機加工藝路線調整,可顯著提升相關軸承及齒輪零組件表面改性滲層硬度一致性。
除 Latrobe Specialty Steel Company 研發的 CSS-42L,美國西北大學 Olson 教授通過計算材料學研發設計出新型耐溫滲碳齒輪鋼,經 Quest Tek Innovations LLC 及 Carpenter Technology 公司產業化后,在美國五代機中得到推廣應用,相關合金體系以 Ferrium 命名。該合金系列中除目前已知的Ferrium C61(AMS6517)、Ferrium C64(AMS6509) 和 Ferrium C69 及 Ferrium CS62 四種滲碳齒輪鋼之外,還有 Ferrium N63 高溫氮化用齒輪鋼(基于 1Cr13 馬氏體不銹鋼)、Ferrium S53(AMS5922)超高強度耐蝕結構鋼、Ferrium M54(AMS6516)高強度耐蝕結構鋼(疲勞性能和應力腐蝕門檻值 Kiscc 顯著優于 AerMet 100)。
Ferrium 合金體系中,隨著 Cr、Mo 含量的增加,滲層組織改性后的硬度相應增加。Ferrium C61 是表 3 中四種 Ferrium 滲碳鋼滲碳表面改性后滲層組織硬度最低的牌號。為進一步提升滲層組織的硬度及耐磨性,在 Ferrium C61 母合金基礎之上,采取適量增加 Mo 合金含量、提高滲層組織二次特殊碳化物析出體積分數的方式,衍生出 Ferrium C64。
美國材料體系中,9310、Pyrowear 53 和 Ferrium C61/C64 三代齒輪鋼同屬低碳合金鋼,強韌性匹配呈現出典型的迭代提升,且在相應代際的材料體系中,抗沖擊韌性均表現優異。Ferrium C61 強度與斷裂韌度優于 Ferrium C64,用于替代現有 9310 鋼,制造直升機旋翼軸類零件;Ferrium C64 滲碳后滲層表面硬度高于 Ferrium C61,更適于制造對耐磨性需求更高的齒輪材料,用于替 Pyrowear 53 鋼,以期進一步提升齒輪的耐溫特性。
上述材料間呈現出顯著的指向性代際替換,力學性能對比見表 4。國內王旭團隊開展了 Ferrium C61、Ferrium C64 熱處理工藝制度研究工作,目前為止尚未發現有關滲碳表面改性方面的文獻報道。相對 CSS-42L 合金體系而言,Ferrium C61/C64 兩個牌號滲碳改性后,雖然強韌性得到大幅提升,但滲碳改性層的硬度仍相對較低,不能滿足超高接觸疲勞工況服役下的耐久性技術要求。
表 4 9310、Pyrowear 53 和 Ferrium C61 常規熱處理后的室溫力學性能
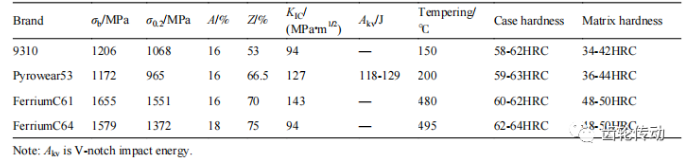
Quest Tek Innovations LLC 在 Ferrium C61/C 64 合金基礎之上,大幅增加 Cr、Mo、Co 合金化元素含量,研制出 Ferrium C69,滲碳改性后,滲層表面顯微硬度高達 HV0.3950(≥HRC68),與 CSS- 42L 滲碳改性后的滲層表面硬度數值接近。表 3 中的 Ferrium C69 合金體系中,(Cr+Mo)含量僅為(5+5)%,顯著低于 CSS-42L 中的(14+4.75)%,這種數值差異,將會顯著影響其滲層組織特殊碳化物析出形態及脈沖工藝控制方法,與此同時,Ferrium C69 合金體系中的 Co 含量過高,在合金化熔煉及經濟性方面并不突出。
第三代滲碳齒輪鋼含有大量的 Cr、Mo 強碳/氮化物形成元素,化學表面改性工藝可設計性極強,通過特定的表面改性工藝方法,調控滲層組織原位析出的碳化物形態,提高滲層組織疲勞性能,將是未來第三代滲碳齒輪鋼能否實現規模化工程應用的主要研究方向。
四、滲碳齒輪鋼的未來發展趨勢
第一代滲碳齒輪鋼,心部組織淬火后,從板條馬氏體中析出 Fe3C 型碳化物,第二代滲碳齒輪鋼,心部組織淬火后,基體會有少量“二次硬化”現象析出的特殊碳化物,從而部分增強基體耐熱性。第三代滲碳齒輪鋼因強碳化物形成元素種類多、含量高,心部組織的“二次硬化”現象占據主體。
在第三代滲碳齒輪鋼中,冶金學家利用計算材料學手段,綜合考量各種強韌化機理,將合金鋼中的“二次硬化”機理應用到極致,已經充分發揮出合金化元素 Mo 在“二次硬化”過程中產生的 M2C 析出強化效果,通過合金化種類及含量的調整,第三代滲碳齒輪鋼服役溫度的提高效果不再顯著。
超高強度將是第三代滲碳齒輪鋼未來的一個發展方向。實現超高強度的一個主要路徑,是采取基體增碳的方式,相關材料見表 5。基體碳含量增加后,M2C 析出的體積分數會顯著增加,根據材料物相的復合定律,基體的強度與硬度會同步增加,有效提升基體的比強度,進而實現齒輪設計與制造的減重。
表 5 航空用超高強度鋼 Ferrium S53、AerMet310 及 CH 2000 冶金成分對比(質量分數/%)
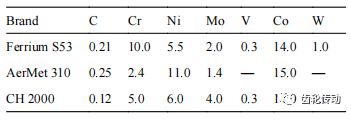
以 Ferrium S53 超高強度鋼為例,該合金組分及主合金化元素含量與 CSS-42L極為相似,CSS- 42L 為臨界超高強度鋼,碳含量由 CSS-42L 的 0.15% 提升至 0.21% 之后,抗拉強度可達 1900 MPa 以上,抗拉強度與屈服強度均提升 100 MPa 以上,但基體增碳后,會犧牲部分基體韌性。合金鋼中另一種強化基體的主要方式,相間沉淀硬化也面臨著同樣問題,相間彌散、沉淀析出的耐熱金屬間化合物 Ni3(Al、Ti、Mo、Nb)、NiAl、Fe2Mo 等,沉淀析出的溫度范圍與“二次硬化”時效溫度范圍幾乎重疊,強化效果相近。
在現有高 CoNi 系第三代滲碳齒輪鋼合金體系下,合理調增 Mo 元素的含量,將是新型第三代滲碳齒輪鋼的一種重要發展方向,采用該路徑設計合金體系,有助于實現“二次硬化”與“沉淀硬化” 兩種強化機制的疊加,從而進一步提升第三代滲碳齒輪鋼的強度。同時,為了獲得相對較好的容限損傷能力,基體中的碳含量應進一步降低。
國產 CH 2000 與 Ferrium S53 兩種超高強度鋼的合金化設計原理基本一致,CH 2000 雖然碳含量不及 Ferrium S53,但其 Mo 含量顯著增多,能夠沉淀更多的彌散金屬間化合物,釘扎位錯強化的效果更為突出,因此,CH 2000 的抗拉強度顯著高于 Ferrium S53,與 AerMet 310 相當,抗拉強度接近 2200 MPa。
相間沉淀與“二次硬化”均存在峰時效,彌散析出與基體共格、半共格的納米尺度高模量強化相、有效釘扎位錯、激發位錯增殖,形成局域高應力場,最終增強基體。兩種強化機制產生的強化 相,在尺度方面無顯著差異,強化效果主要取決于析出相的體積分數差異。“二次硬化”涉及基體碳含量及 Mo、W、V、Ti、Nb、Ta、Zr 等強碳化物形成元素的含量,齒輪服役時存在較大沖擊載荷,因此,滲碳齒輪鋼碳含量普遍偏低(≤0.20%),強碳化物形成元素在鋼中的添加總量通常也會受到嚴格控制。
沉淀硬化鋼中的主合金化元素 Ni 含量通常在 2% 以上,且在一定范圍內,Ni 含量越高沉淀硬化效果越好。沉淀析出與“二次硬化”析出,均需遵守相應的動力學,產生沉淀硬化的 Ni 與 Mo 等沉淀相元素濃度乘積數值顯著高于“二次硬化”析出的 C 與 Mo 等強碳化物形成元素濃度乘積數值,宏觀表現出更高的強化能力。因此,通過“沉淀硬化”機制進一步提升基體強度,將是未來第三代滲碳齒輪鋼新型鋼種研制的一個主要方向。
第三代滲碳齒輪鋼中的強碳化物形成元素 W、V、Ti、Zr、Nb、Ta 等含量相對較低,通過提升基體內的強碳化物形成元素含量,可適當將基體“二次硬化”溫度范圍向更高溫區推動,受基體再結晶軟化的影響,服役溫度提升有限。
“二次硬化”與“沉淀硬化”兩種強化機制均存在過時效問題,過時效溫區與基體 α 相再結晶重疊,過高的時效/回火處理溫度,會加速基體強度的快速衰減,因此,通過上述兩種強化機制大幅提升材料的服役溫度,理論上不具可行性。
第四代滲碳齒輪鋼尚未有相關文獻報道,在文獻中提到第四代滲碳軸承鋼 60NiTi 及 GCr15Al 尚處于研發階段。60NiTi 鎳基合金由美國海軍軍械實驗室于 20 世紀 50 年代研制,通過時效析出硬質 Ni4Ti3 納米析出相強化基體,該材料在不同熱處理狀態下的硬度值跨度為 32~63HRC,雖然其耐蝕、耐磨性均顯著優于 440C(對應國產牌號 9Cr18Mo),密度低且無磁性(6.7 g/cm3 ),但其機械加工難度大,NASA 標定的最高服役溫度僅為 400 ℃,與第三代滲碳齒輪鋼服役溫度相當,僅能用于特定技術需求的齒輪制造。
在 500 ℃ 以上更高溫區服役,合金鋼不但要考慮自身強度及耐熱性問題,還要考慮高溫氧化問題,雖然理論層面很難預測下一代耐高溫滲碳齒輪鋼是否存在,但 500 ℃ 以上服役的齒輪材料必須具有非常優異的高溫抗氧化特性,同時兼顧一定的熱強性與經濟性,2000 系列鐵基高溫合金最有可能成為備選基礎合金材料體系。通過合金成分優化設計,合理引入 Co 元素、增加可形成 Ni3M(M 為 Ti、Mo、Al、Nb 等)沉淀硬化相的 M 元素含量,形成高 Cr 高 Ni 超合金化的鐵基合金,合金體系中的高 Cr 含量,將會給滲碳表面強化帶來極大難度。
五、結束語
航空齒輪選材對航空動力傳動系統的可靠性至關重要,需要綜合考量服役溫區、傳遞載荷大小及經濟適用性三者間的匹配。現有滲碳齒輪鋼主要以服役溫區進行代際劃分,材料的代際間性能提升,需兼顧滲層與基體兩者間的強化方式與效果。
(1)第一代滲碳齒輪鋼為低碳中低合金鋼,滲層組織以 Fe3C 型碳化物強化,基體回火抗力差,整體服役溫區≤200 ℃,16Cr3NiWMoVNbE 可通過工藝優化跨代提升至第二代滲碳齒輪鋼。
(2)第二代滲碳齒輪鋼為低碳中高合金鋼,滲層組織仍以 Fe3C 型碳化物強化為主,因合金體系中合金化程度增高、強碳化物形成元素增多,基體回火過程中可析出部分時效相,提高基體回火抗力,整體服役溫區≤350 ℃。
(3)第三代滲碳齒輪鋼為低碳超高合金鋼,根據合金設計體系,超高 Cr-Co-Mo 系滲層組織以二次特殊碳化物形式析出,強烈硬化滲層組織,超高 Ni-Co 系滲層組織二次碳化物析出量大幅降低,滲層組織硬化效果不顯著。
(4)第三代滲碳齒輪鋼充分利用“二次硬化”機制強化基體,使其能夠在 500 ℃ 以下溫區長期服役。輔助“沉淀硬化”可大幅提升基體強度,相關強化機理可用于指導新型耐高溫超高強度滲碳齒 輪鋼開發。
(5)受合金化元素在鋼中擴散激活能影響,“二次硬化”與“沉淀硬化”強化機制存在上限溫區,與基體 α 相再結晶溫區毗鄰,因此,現有合金結構鋼體系難于通過成分優化設計,有效避免 500 ℃ 以上高溫長期服役存在的強度快速衰減。
參考文獻略.